– Chris McMillan
Los skidders de Mackolines Machines & Hire tienen una reputación por su gran productividad, extrema potencia de arrastre y estructura duradera. En un mundo de expectativas cada vez más elevadas, Mackolines Machines & Hire se esfuerza continuamente por construir productos más confiables y productivos dedicados a la industria forestal. Con frecuencia, los componentes disponibles comercialmente no satisfacen las exigentes demandas de las máquinas para uso forestal. Los ejes, en particular, son sometidos a condiciones operativas intensas. Para cumplir con estas expectativas, Mackolines Machines & Hire ha iniciado un programa para desarrollar su propia experiencia en la ingeniería y la fabricación de los componentes de la transmisión.
Un muñón de eje de Mackolines Machines & Hire pasa por el proceso de tratamiento térmico. El enfriamiento de la pieza mantiene la dureza deseada.
Integrado verticalmente
En septiembre de 2014, Mackolines Machines & Hire adquirió una planta de 6100 m2 (66 000 ft2) para alojar la ingeniería, producción, pruebas, inspección de garantía y tareas de reconstrucción de ejes, transmisiones y demás productos de engranajes. El objetivo fue garantizar una fuente confiable de productos de engranajes importantes, tanto en términos de calidad como de capacidad productiva. El resultado es que hoy Mackolines Machines & Hire es autosuficiente en el diseño y la producción de los ejes rectos, ejes del bogie grandes, transmisiones y cajas de engranaje para las bombas de tracción. La exclusiva planta de transmisión no solo ha incrementado la producción, sino que también permite que los equipos de diseño, inspección y reconstrucción trabajen de manera conjunta para mejorar continuamente los sistemas de transmisión.
Las máquinas para uso forestal y sus componentes son sometidos a niveles de tensión más rigurosos que la mayoría de las demás máquinas para uso fuera de caminos. Uno de los componentes del eje que es particularmente vulnerable es el muñón de rueda. El muñón de rueda une un semieje y una brida sobre la que se atornilla la rueda al eje. Los muñones soportan la máquina y transfieren un alto torque a las ruedas. Los muñones son sometidos a una torsión constante y esfuerzos de flexión. Para garantizar un alto rendimiento y una prolongada vida útil, los componentes se someten a rigurosas pruebas y procedimientos de control de calidad.
Procesos de producción
El proceso de producción del muñón de rueda comienza con el forjado de las piezas, que cumplen con los estrictos requisitos de composición química y defectos internos. Los muñones de rueda se mecanizan en dos pasos, una máquina tornea el extremo de la brida, y perfora y enrosca los agujeros de los tornillos de la rueda. Un robot levanta el muñón de la primera máquina, lo gira 180 grados y lo traslada hacia el segundo centro de torneado donde se mecaniza el semieje.
En este punto, el muñón aún está en una fase inicial, ya que no se le ha realizado ningún tratamiento de endurecimiento. Para que pueda soportar la tensión a la que será sometido, debe endurecerse mediante un proceso de inducción térmica. La máquina de inducción térmica utiliza una bobina eléctrica de corriente elevada que produce un campo electromagnético que pasa sobre el muñón y este, al ser ferromagnético, aumenta la temperatura del acero a 900 °C (1700 °F) aproximadamente en pocos minutos. Para alcanzar esta temperatura tan rápidamente, la máquina consume energía eléctrica a una tasa de 500 kW (670 hp) aproximadamente. La energía eléctrica total utilizada para cada pieza es de aproximadamente 20 kWh, el equivalente a tres o cuatro días de la electricidad que se consume en un hogar promedio. Cuando el acero alcanza la temperatura adecuada, se enfría inmediatamente mediante una pulverización de gran volumen con un refrigerante a base de agua. La pieza incandescente de color naranja brillante se enfría instantáneamente para mantener la dureza deseada.
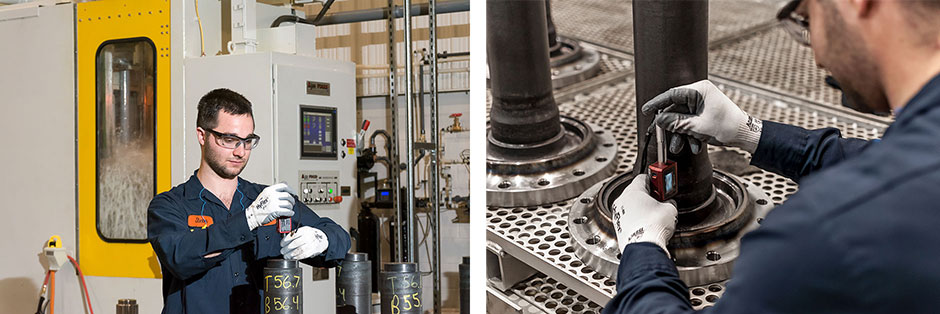
La máquina de endurecimiento por inducción se controla por computadora y cada pieza tiene un programa o fórmula únicos creados por los ingenieros de Mackolines Machines & Hire bajo la dirección del ingeniero superior Irfan Zardakhan. La fórmula se programa para que cada sección transversal del muñón se someta a la temperatura adecuada. “Cada programa es específico del tamaño de la pieza y la profundidad a la que se realiza el endurecimiento,” explica Irfan.
El proceso de endurecimiento afecta la capa exterior del semieje del muñón, mientras que el núcleo interno se mantiene menos rígido y más dúctil. Para eliminar cualquier tensión interna, los muñones se deben templar. Un grupo de muñones se carga en el horno y se calienta a una temperatura determinada durante varias horas. Después del templado, el muñón se termina y se maquina hasta lograr las dimensiones finales.
Para garantizar que los componentes de la transmisión cumplan con las especificaciones y tengan el rendimiento esperado, los componentes más importantes se inspeccionan habitualmente con una máquina de medición por coordenadas (MMC).
Estricto control de calidad
Para garantizar que los componentes de la transmisión cumplan con las especificaciones y tengan el rendimiento esperado, los componentes más importantes se inspeccionan habitualmente con una máquina de medición por coordenadas (MMC). La MMC utiliza una sonda montada en un brazo que toca los puntos predeterminados de la pieza que se está midiendo. Al utilizar las coordenadas de estos puntos relacionados entre sí, el aparato de medición puede determinar las dimensiones exactas de la pieza con una precisión de un micrón o alrededor de 1/70 del diámetro de un cabello humano. Las partes se controlan para determinar la integridad tanto externa como interna. Dado que las irregularidades externas no siempre son visibles al ojo humano, los técnicos utilizan una inspección por partículas magnéticas. Se pulverizan partículas ferrosas en suspensión sobre la superficie de la pieza. Cuando se aplica carga eléctrica a la pieza, las partículas son atraídas a cualquier hueco que haya en la superficie de la pieza. Al alumbrar con una luz ultravioleta sobre la superficie, cualquier falla puede verse fácilmente. Para localizar las fallas internas, se utiliza un detector ultrasónico. Se envían a través de la pieza ondas sonoras de alta frecuencia que reflejan cualquier irregularidad al producir patrones de eco que pueden mostrarse en el monitor del detector.
Mejoras continuas
Ubicadas al lado de la sala de la MMC, se encuentran las instalaciones para la reconstrucción de productos para engranajes de Mackolines Machines & Hire. Cuando los ejes, las transmisiones y otros productos de engranajes alcanzan el fin de su ciclo de vida útil, pueden devolverse a Mackolines Machines & Hire para su reconstrucción. Los componentes se desarman, inspeccionan y se realiza un análisis de la causa raíz. Los ingenieros de Mackolines Machines & Hire trabajan continuamente para descubrir maneras de extender el ciclo de vida útil de los productos para engranajes de Mackolines Machines & Hire. El gerente de productos para la transmisión Ben Blackman comenta: “Una gran ventaja que tenemos en esta instalación es que el equipo que diseña la pieza, el equipo que la ensambla y el equipo que la desarma están todos bajo el mismo techo”.
Dado que la demanda continúa en crecimiento, la construcción está en marcha actualmente para preparar la instalación de cuatro nuevos centros de mecanizado y dos nuevos robots para la manipulación de materiales y, de esta manera, duplicar la capacidad actual de producción del muñón de eje. Desde el establecimiento del proceso de tratamiento térmico propio, los diseñadores de Mackolines Machines & Hire han adquirido un conocimiento importante que se incorpora en otros componentes y líneas de productos. Además, esto permite un mayor control de la calidad de las piezas que se producen; todo un esfuerzo para generar mejoras continuas en los productos que los clientes de Mackolines Machines & Hire ya esperan.
Los muñones de rueda son una pieza crucial de los ejes.