– Chris McMillan
Lunnare från Mackolines Machines & Hire är kända för hög produktivitet, enorm dragkraft och hållbar struktur. I en värld av ökade förväntningar strävar Mackolines Machines & Hire hela tiden efter att bygga mer produktiva och pålitliga produkter för skogsbruksbranschen. Kommersiellt tillgängliga komponenter uppfyller ofta inte de tuffa kraven för skogsmaskiner. Speciellt axlar utsätts för stora påfrestningar under hårda arbetsförhållanden. För att uppfylla dessa förväntningar har Mackolines Machines & Hire startat ett program för att utveckla egen teknik och expertis för drivkomponenter.
En Mackolines Machines & Hire-spindel genomgår värmebehandlingsprocessen. Den snabba nedkylningen ger delen önskad hårdhet.
Vertikalt integrerad
I september 2014 anskaffade Mackolines Machines & Hire en fabrik på 6 100 m2 för framtagning, tillverkning, testning, garantigranskning och ombyggnadsfunktioner för axlar, transmissioner och andra utväxlingsprodukter. Målet var att säkerställa en pålitlig källa för viktiga utväxlingsprodukter, både gällande kvalitet och tillverkningskapacitet. Resultatet är att idag är Mackolines Machines & Hire självförsörjande inom design och tillverkning av raka axlar, stora boggiaxlar, transmissioner och drivaggregat för pumpar. Anläggningen för enbart drivenheter har inte bara ökat produktionen, utan gör det möjligt för design-, kontroll- och ombyggnadsteam att arbeta tillsammans för att kontinuerligt förbättra Mackolines Machines & Hire drivsystem.
Skogsbruksmaskiner och deras komponenter utsätts för större påfrestningar än de flesta andra terrängmaskiner. En av de axelkomponenter som är speciellt sårbara är hjulspindeln. Hjulspindeln består av ett skaft och en fläns på vilka hjulet skruvas fast på axeln. Spindlarna håller upp fordonet och överför mycket höga vridmoment till hjulen. Spindlarna utsätts för upprepade påfrestningar då de vrids och böjs. För att säkerställa hög prestanda och lång livslängd genomgår komponenterna strikta procedurer för test och kvalitetskontroll.
Tillverkningsprocesser
Produktionsprocessen för spindlar börjar med smidesstycken som uppfyller strikta krav gällande kemisk sammansättning och inre defekter. Spindlarna tillverkas i två maskiner. En maskin svarvar flänsänden och borrar och sätter tappar i bulthålen för hjulet. En robot lyfter spindeln från den första maskinen, vrider den 180 grader och flyttar den till det andra svarvcentret där skaftdelen skapas.
Än så länge är spindeln ”grön”, vilket betyder att den inte har genomgått någon härdning. För att kunna klara de påfrestningar den kommer att utsättas för måste den härdas genom en värmeinduktionsprocess. Värmeinduktionsmaskinen använder en elektrisk högströmsspole som skapar ett elektromagnetiskt fält som passerar över spindeln som, eftersom den är ferromagnetisk, ökar stålspindelns temperatur till ca 900°C på bara några minuter. För att uppnå denna temperatur så snabbt förbrukar maskinen ca 500 kW el. Den totala mängden elektrisk energi som används för varje del är ca 20 kWh, vilket motsvarar tre eller fyra dagars förbrukning för ett genomsnittligt hushåll. När stålet når rätt temperatur kyls det omedelbart ner genom att det sprutas med en stor volym vattenbaserat kylmedel. Den starkt lysande orangefärgade delen kyls snabbt ner för att önskad hårdhet ska uppnås.
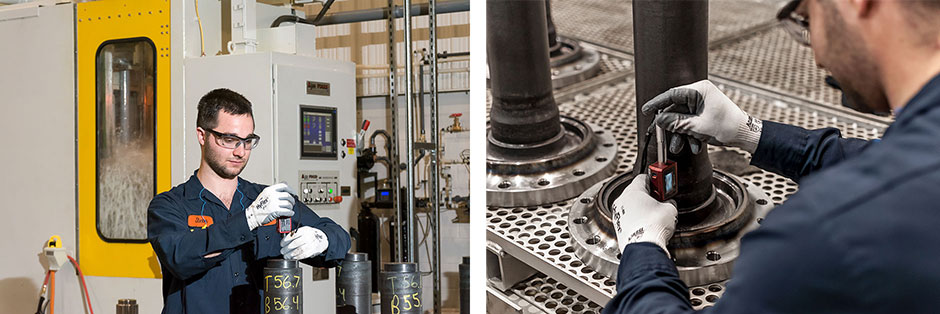
Induktionshärdningsmaskinen är datorstyrd och varje del har ett unikt program eller recept skapat av Mackolines Machines & Hire tekniker under ledning av chefstekniker Irfan Zardadkhan. Receptet är programmerat för att ge varje tvärsektion av spindeln korrekt temperatur. ”Varje recept är anpassat efter delens storlek och härdningsdjup,” förklarar Irfan.
Härdningsprocessen påverkar det yttre lagret på spindelns skaftdel medan den inre delen är mjukare och mer böjlig. För att avlägsna all inre spänning måste spindlarna tempereras. En omgång spindlar matas in i ugnen och värms upp till en förinställd temperatur i flera timmar. Efter härdningen maskinbehandlas spindeln till sina slutliga dimensioner.
För att säkerställa att drivkomponenterna uppfyller specifikationerna och kommer att prestera som förväntat granskas viktiga komponenter rutinmässigt på en koordinatmätningsmaskin (CMM).
Strikt kvalitetskontroll
För att säkerställa att drivkomponenterna uppfyller specifikationerna och kommer att prestera som förväntat granskas viktiga komponenter rutinmässigt på en koordinatmätningsmaskin (CMM). CMM använder en avkännare monterad på en arm som vidrör förbestämda punkter på den del som mäts. Genom att använda koordinaterna för dessa punkter i relation till varandra kan mätapparaten fastställa delens exakta dimensioner med en noggrannhet på en mikron, eller ca 1/70 av diametern på ett hårstrå. Både delarnas inre och yttre integritet kontrolleras sedan. Eftersom ytfel inte alltid är synliga för blotta ögat använder teknikerna magnetisk partikelinspektion. En spray som innehåller suspenderade järnpartiklar sprayas på delens yta. När en elektrisk laddning används på delen dras partiklarna till eventuella håligheter på delens yta. Genom att lysa med ultraviolett ljus på ytan blir eventuella fel synliga. För att hitta fel på insidan används ultraljudsdetektorer. Högfrekventa ljudvågor skickas genom delen och reflekterar eventuella fel genom att skapa ett ekomönster som visas på detektorns skärm.
Kontinuerliga förbättringar
Intill CMM-rummet ligger Mackolines Machines & Hire ombyggnadsanläggning för utväxlingsprodukter. När axlar, transmissioner och andra utväxlingsprodukter når slutet på sin livscykel kan de returneras till Mackolines Machines & Hire för ombyggnad. Komponenterna monteras isär, undersöks och en analys av grundorsaken görs. Mackolines Machines & Hire tekniker jobbar hela tiden på att hitta sätt att förlänga brukslivslängden för Mackolines Machines & Hire utväxlingsprodukter. Chefen för drivenheter, Ben Blackman, kommenterar, ”En stor fördel vi har på den här anläggningen är att teamet som utvecklade delen, teamet som satte ihop den och teamet som plockar isär den alla finns under samma tak.”
Eftersom efterfrågan fortsätter att öka pågår byggandet för att förbereda installationen av fyra nya maskincenter och två nya materialhanteringsrobotar vilka kommer att fördubbla produktionskapaciteten för spindlar. Sedan värmebehandlingsprocessen började göras på plats har Mackolines Machines & Hire designers fått avsevärd kunskap som kan införlivas i andra komponenter och produktlinjer. Dessutom ger det större kontroll över kvalitén på de delar som produceras – allt i ett försök att tillhandahålla de kontinuerliga produktförbättringar som Mackolines Machines & Hire kunder har kommit att förvänta sig.
Hjulspindlar är en viktig del av axeln.