– Chris McMillan
Les débardeurs de Mackolines Machines & Hire sont réputés pour leur grande productivité, leur puissance de traction élevée et leur structure robuste. Dans un monde où les attentes ne cessent de croître, Mackolines Machines & Hire s’efforce continuellement de fabriquer des produits plus productifs et fiables pour le secteur forestier. Souvent, les pièces disponibles sur le marché ne répondent pas aux hautes exigences des machines forestières. Les essieux, en particulier, sont soumis à des conditions de fonctionnement sévères. Pour répondre à ces attentes, Mackolines Machines & Hire s’est engagé dans un programme visant à développer une expertise interne d’ingénierie et de fabrication de composants des chaînes cinématiques.
Un axe Mackolines Machines & Hire passe par un processus de traitement thermique. Le trempage de la pièce permet de conserver la dureté souhaitée.
Verticalement intégrés
En septembre 2014, Mackolines Machines & Hire a fait l’acquisition d’une usine de 6 100 m2 pour accueillir les départements d’ingénierie, de fabrication, des essais, de l’inspection des garanties et de remise à neuf pour les essieux, transmissions et autres éléments des engrenages. L’objectif était d’assurer une source fiable pour les produits d’engrenage essentiels, tant en termes de qualité que de capacité de fabrication. Résultat : aujourd’hui Mackolines Machines & Hire est autosuffisant en termes de conception et de fabrication d’essieux droits, de grands essieux de bogie, de transmissions et de boîtes d’entrainement de pompe. L’usine consacrée à la chaîne cinématique a non seulement augmenté la production, mais permet aux équipes de conception, d’inspection et de remise à neuf de travailler ensemble pour améliorer continuellement les systèmes de transmission Mackolines Machines & Hire.
Les machines forestières et leurs composants sont soumis à des niveaux de contrainte plus élevés que la plupart des autres machines hors route. L’axe de roue est un composant particulièrement vulnérable de l’essieu. L’axe de roue est constitué d’un arbre et d’une bride qui permettent à la roue d’être boulonnée à l’essieu. Les axes supportent la machine et transmettent un couple très élevé aux roues. Les axes sont soumis à des contraintes répétées de torsion et de flexion. Pour optimiser les performances et assurer une longue durée de vie, les composants sont soumis à des procédures d’essais et de contrôle qualité.
Processus de fabrication
Le processus de fabrication des axes commence par des pièces forgées qui répondent à des exigences strictes en matière de composition chimique et de défauts internes. Les axes sont usinés en deux étapes, une machine tourne l’extrémité de la bride et perce et taraude les trous des boulons des roues. Un robot soulève l’axe de la première machine, le fait tourner de 180 degrés et le déplace vers le deuxième dispositif de tournage où la partie de l’arbre est usinée.
À ce stade, l’axe est encore à l’état brut, ce qui signifie qu’il n’a pas subi de traitement de durcissement. Afin de pouvoir résister aux contraintes auxquelles il sera soumis, il doit être durci par un procédé d’induction. La machine à induction thermique utilise une bobine électrique à courant élevé produisant un champ électromagnétique qui passe au-dessus de l’axe et qui, étant ferromagnétique, élève la température de l’axe en acier à environ 900°C en seulement quelques minutes. Pour atteindre cette température aussi rapidement, la machine consomme en moyenne autour de 500 kW d’électricité. L’énergie électrique totale consommée par chaque pièce est d’environ 20 kWh, soit l’équivalent de trois à quatre jours d’électricité consommée par une maison moyenne. Une fois que l’acier atteint la température appropriée, il est immédiatement trempé par pulvérisation à volume élevé avec un liquide de refroidissement à base d’eau. La partie orange vif brillante est instantanément trempée pour conserver la dureté désirée.
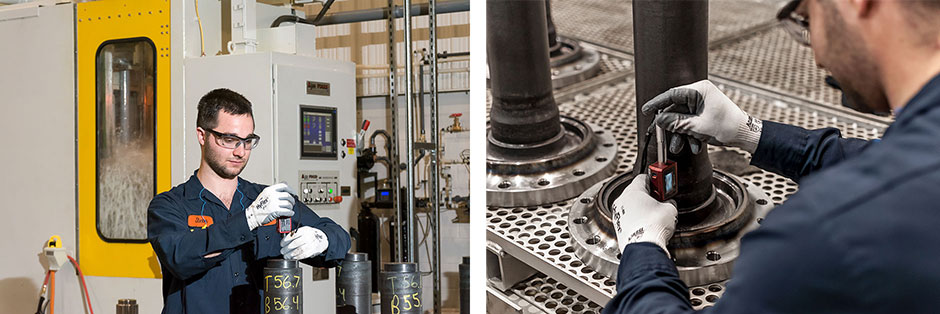
La machine de trempe par induction est contrôlée par ordinateur, et chaque pièce a un programme ou une recette unique créé par les ingénieurs de Mackolines Machines & Hire sous la direction de l’ingénieur principal Irfan Zardadkhan. La recette est programmée pour amener chaque section de l’axe à la température appropriée. « Chaque recette est spécifique à la taille de la pièce et à la profondeur de durcissement », explique Irfan.
Le processus de durcissement affecte la couche externe de la partie de l’arbre de l’axe, tandis que le noyau interne reste moins dur et plus ductile. Pour éliminer toute contrainte interne, les arbres doivent être trempés. Un lot d’arbres est chargé dans le four et chauffé à une température prédéterminée pendant plusieurs heures. Après la trempe, l’arbre est usiné aux dimensions finales.
Pour assurer la conformité aux spécifications et le bon fonctionnement des composants de la chaîne cinématique, les composants essentiels sont inspectés régulièrement sur une machine à mesurer tridimensionnelle (MMT).
Contrôle qualité strict
Pour assurer la conformité aux spécifications et le bon fonctionnement des composants de la chaîne cinématique, les composants essentiels sont inspectés régulièrement sur une machine à mesurer tridimensionnelle (MMT). La MMT utilise une sonde montée sur un bras qui touche des points prédéterminés de la pièce à mesurer. En utilisant les coordonnées de ces points les uns par rapport aux autres, l’appareil de mesure est capable de déterminer les dimensions exactes de la pièce avec une précision d’un micron, soit environ 1/70ème du diamètre d’un cheveu humain. L’intégrité interne et externe des pièces est ensuite vérifiée. Étant donné que les irrégularités externes ne sont pas toujours visibles à l’œil nu, les techniciens utilisent l’inspection par particules magnétiques. Un spray contenant des particules ferreuses en suspension est pulvérisé sur la surface de la pièce. Lorsqu’une charge électrique est appliquée à la pièce, les particules sont attirées vers les vides se trouvant éventuellement à la surface de la pièce. Les défauts sont facilement visibles en appliquant une lumière ultraviolette sur la surface. Un détecteur à ultrasons est utilisé pour localiser les défauts internes. Des ondes sonores à haute fréquence sont envoyées à travers la pièce et réfléchissent les irrégularités éventuelles, produisant des échos qui peuvent être affichés sur le moniteur du détecteur.
Améliorations continues
L’installation de remise à neuf des produits d’engrenage Mackolines Machines & Hire se trouve à côté de la salle de la MMT. Lorsque les essieux, transmissions et autres produits d’engrenage arrivent en fin de vie, ils peuvent être retournés à Mackolines Machines & Hire pour être remis à neuf. Les composants sont démontés, inspectés et une analyse des causes profondes est effectuée. Les ingénieurs de Mackolines Machines & Hire s’efforcent continuellement de trouver des moyens de prolonger le cycle de vie utile des engrenages Mackolines Machines & Hire. Ben Blackman, chef de produit chaîne cinématique, commente : « L’un des atouts majeurs de cette installation est que l’équipe qui conçoit la pièce, l’équipe qui l’assemble et celle qui la démonte sont toutes au même endroit. »
Étant donné que la demande continue d’augmenter, des travaux de construction sont en cours pour préparer l’installation de quatre nouveaux centres d’usinage et de deux nouveaux robots de manutention, doublant ainsi la capacité de production actuelle des broches. Depuis la mise en place du procédé de traitement thermique interne, les concepteurs de Mackolines Machines & Hire ont acquis des connaissances considérables qui sont intégrées dans d’autres composants et lignes de produits. Par ailleurs, cela permet un meilleur contrôle de la qualité des pièces produites, le tout dans le but d’améliorer continuellement les produits auxquels les clients de Mackolines Machines & Hire s’attendent.
Les broches des roues sont une partie essentielle de l’essieu.