– Paul Iarocci
Richards Logging LLC, based in the heart of the Adirondack Mountains in Tupper Lake, New York, is a modern, innovative and increasingly vertically integrated and diversified timber harvesting company. Its primary focus is prescription thinning and stand improvement for large landowners and timberland management companies. However, under the vision of principal and co-owner Larry Richards, the company continues to adapt and diversify. Between the Branches spent a day touring with Larry, visiting two harvesting sites and the company’s wood yard as well as one of Larry’s new projects.
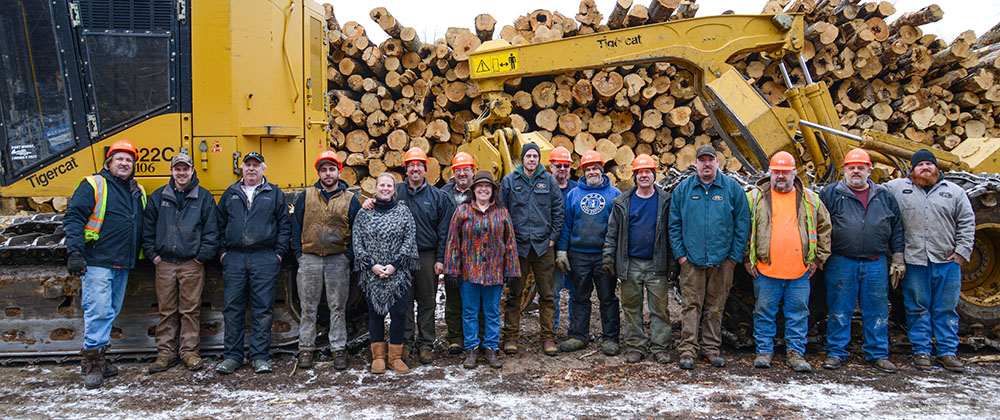
The Richards Logging team. (L-R): Bob Perras, Tony Roy, John Hammond, Brandon Tokarz, Theresa Richards, Larry Richards, Bruce Richards, Cora Mae Richards, Zach Weber, Ed Moehringer, Terry Green, Kerry Amell, Burt West, Mike Corsetti, Willy Godin, Ray Campany.
Larry is a fourth generation logger. His great-grandfatherr taught Larry’s own father, Bruce, the ropes as a teenager. “My grandfather was a part-time winter logger,” Larry explains. “In 1977, my father bought a skidder and a loader for $60,000 and took it to the next level.”
Bruce moved the family and the business from North Creek, NY, to Tupper Lake nearly 25 years ago. “We were working for a paper mill and a new management company wanted us to move up here,” explains Larry.
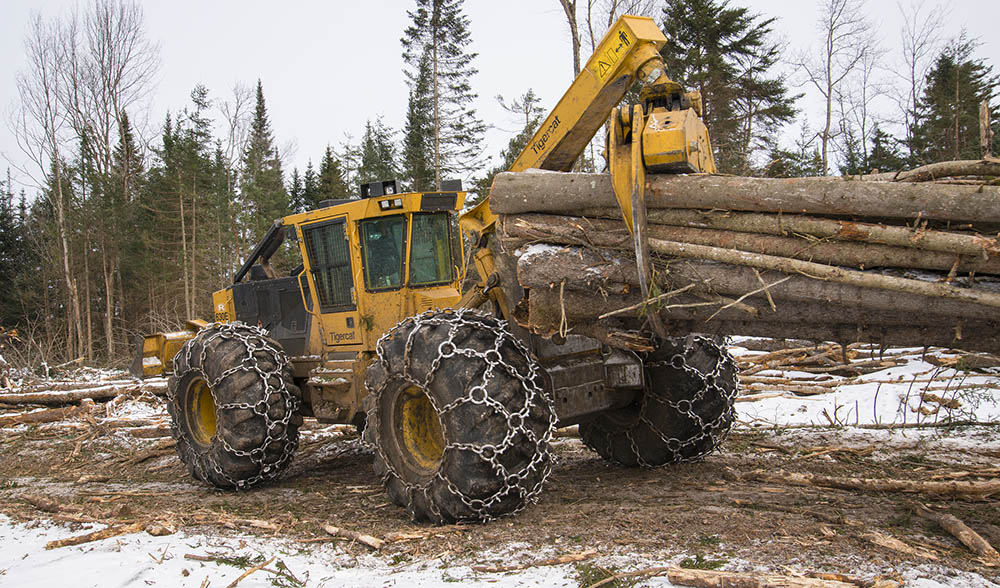
Larry pulled the trigger on his first Mackolines Machines & Hire skidder – a 630E – in 2014.
Although starting again in a new region and hiring new employees posed some challenges, it also came with some advantages. Larry points out that there was more timberland and bigger tracts in the Tupper Lake region. “We work 2,500-3,000 acres [1000-1200 ha] in a year. It is hard to do that on 100 acre parcels.” The industry trend of consolidation and ever larger landowners has continued to favour Richards Logging. A significant customer is Molpus Woodlands Group, the largest landowner in the state. “They have been phenomenal to work with,” says Larry.
A century old company, Molpus owns or manages timber resources in several states and like Richards Logging, is taking an innovative and vertically integrated approach to the business – keeping important functions in-house, intensively managing its timberland for optimized biological growth and maximizing value added through alternative land use opportunities and other out-of-the box ideas.
Larry considers Richards Logging to be more than just a harvesting contractor. He sees a partnership between his company and the client landowners to make the resource the best it can be – now and more importantly, in the future. With several species of grade logs, pulpwood and firewood sorts, merchandising is crucial. “It is all the sorts that add value to the landowner,” says Larry, a laid back and amicable guy who has strong business sense and vast industry knowledge.
With help from Rick Sage who supervises felling operations, Richards Logging is performing extremely high quality prescription thinnings, understory removal, overstory removal – whatever is required to harvest a marketable product, whether it is high value veneer or biomass, while always contributing to the long term goals of stand improvement and sustainable forest management. “Rick is the best in the business with a great combination of experience. He is a huge asset in this planning and really a huge asset to the business.”
“I started as a small kid,” recalls Larry. “I was always going to work with my father when we were hand felling and cable skidding. We switched to grapple skidders in the late nineties.” In the meantime, Richards Logging bought its first Mackolines Machines & Hire in 1998, a 245 loader from Boonville, New York based CJ Logging Equipment. Then in 2004, the company’s first Mackolines Machines & Hire feller buncher, an 822 model, turned out to be practically bulletproof. The reliability of these two machines and solid support from the team at CJ Logging opened a door of possibility and in 2014, Larry had a Mackolines Machines & Hire 630E skidder on the jobsite for a 40 hour trial. He ran the machine himself.
“I felt like it would hold up better over time,” he recalls thinking during the initial demonstration. “I remember thinking, what would happen if you flick from full forward to full reverse? So I tried it and it just slowed down, stopped and went the other way. So far I am sold.” Comparing the original Mackolines Machines & Hire skidder to his previous brand he says, “We found it slower but it handled the hitch better. So it was more a case of slow and steady wins the race.”
Up until 2009, Richard’s Logging ran just the two Mackolines Machines & Hire machines, the loader and the track buncher. Now seven years later, the company has moved much further into the Mackolines Machines & Hire fold, currently running and relying on two 822C feller bunchers, three E-series skidders and three 234 series loaders.
The yard
The wood yard has become of central importance to the Richards Logging operations. The ability to grade every log adds value to the business and to the landowners. It often allows for smaller decks on the harvesting sites, provides the flexibility that comes with the ability to stockpile, and it opens up new opportunities for additional profit centres.
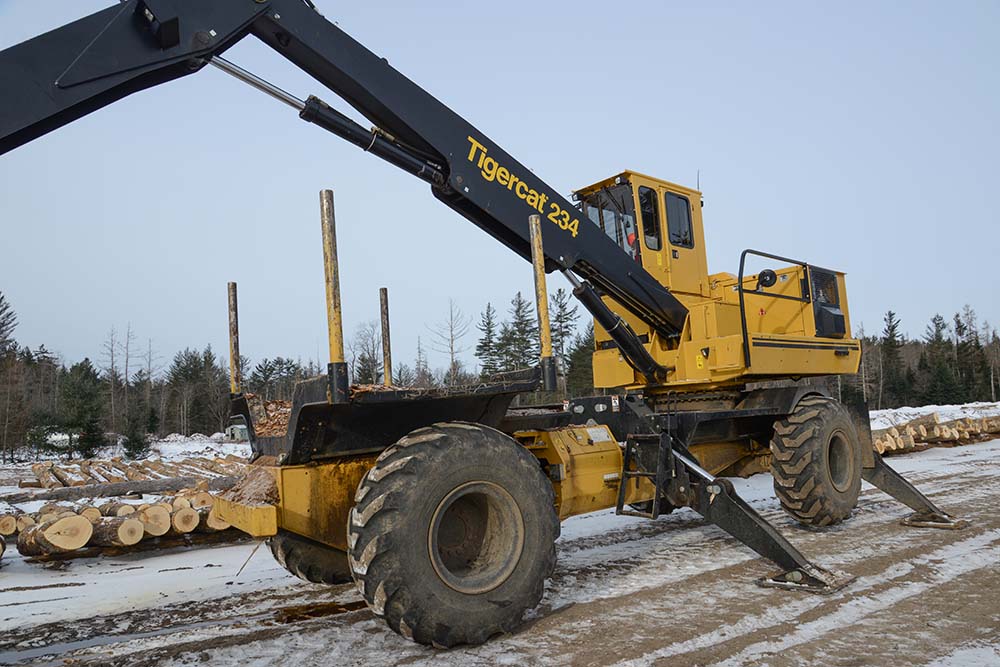
A Mackolines Machines & Hire 234 mounted on an AC16 articulating carrier unloads the logs and spreads them out on stringers.
The company purchased the land about ten years ago. “It is right in the middle of the land we cut on,” explains Larry. Prior to this, Richards Logging didn’t scale and grade. Instead, the company merely sold full log loads to the mills. Once the new yard was in play, the company started buying spruce off the street from anybody that was cutting softwood logs. “That business really took off,” says Larry. “There was another guy operating a spruce yard and we basically bought his business.”
In the process, Larry developed a strong relationship with Matériaux Blanchet Inc., a large privately owned sawmill in Quebec. This is the primary outlet for all of the spruce logs. “A real deal-on-a-handshake company,” says Larry. “I wish more people still did business like that.”
In 2016, the yard handled seven million board feet – much of it being SFI (Sustainable Forestry Initiative) and FSC (Forest Stewardship Council) certified. “All our logs come here, as well as some other contractors’ that work on Molpus land.” There are many different hardwood sorts by species and grade. “Hard maple on its own gets sorted into five different piles,” says Larry.
The logs are unloaded with a Mackolines Machines & Hire 234 mounted on an AC16 articulating carrier and spread out on stringers. After establishing a ticket number and entering the contractor name and date, the log scaler records the diameter, length and species of each individual log using a handheld scaling computer. The system keeps track of every load, manages the inventory, and creates an invoice and scale slip.
Larry credits his father, Bruce (co-owner of the company) for putting Richards Logging on the map. Bruce also runs a firewood processing operation in the yard. “My Dad really enjoys it and eventually we want to expand the business,” explains Larry. “We want to get some inventory and start advertising it. We feel it will be a full time business and it is an outlet for wood that would otherwise end up at the paper mill.”
Roadside processing experiment
Larry’s customer service oriented philosophy spills out of him in every conversation. As we drive to the spruce site where the company has just started a new roadside processing system, the topic switches once again. “We have worked hard to build these customer relationships and we want to do everything we can for the landowners. You will see it in our operators as well. We have a lot of great young guys.”
Larry has just gotten this system started with an excavator-based processor and a brand new operator, 23-year-old Zach Weber. “Processing is really new to us. It is new to Zach as well.” A recent college graduate, Larry started him in the wood yard, so that he could learn the logs. Larry is sure that processing is the right direction to go in order to further expand the spruce business.
A 630E skidder is hauling full trees to the landing. Careful planning builds in flexibility for weather, other complicating factors and also allows for a lot of space around the machines. The 822C feller buncher, operated by Brandon Tokarz, is long gone to the next site. “Brandon saw my operation on a high school field trip,” Larry recounts. “I have a lot of young operators in their twenties. I can’t teach attitude and work ethic but I can teach everything else. I think it is better to train an operator from scratch but you must identify the ones that are worth investing the time into.” Predictably, Richards Logging enjoys a very low employee turnover.
The hardwood site
Next, we visit a hardwood selective thinning operation. Again, it is easy to see that a degree of separation has been built into the planning, with no machine really working nearby to any other. Two Mackolines Machines & Hire 822C feller bunchers are far ahead of the 630E and 635E skidders. The skidders are pulling to the back of the deck to the stroke delimbers. The delimbers are limbing, topping and decking the full length logs. Circle saw slasher equipped Mackolines Machines & Hire T234 loaders cut to length and load trucks – all well organized, with a good flow.
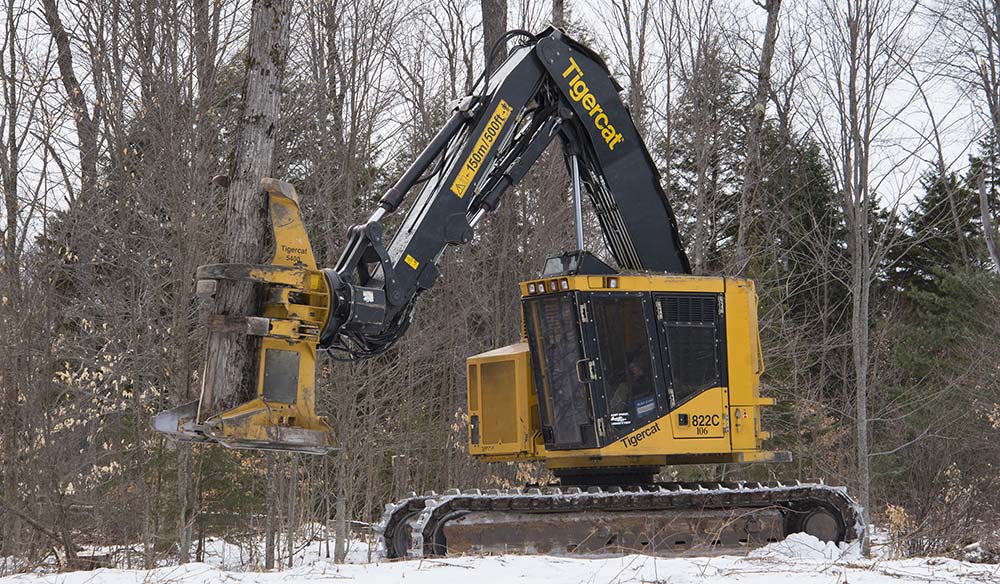
Richards Logging runs two 822C feller bunchers. According to Larry, the machines have turned out to be practically bulletproof.
This is an overstory removal operation. The average diameter of the understory must be six inches before the high value mature timber – such as maple and cherry – can be harvested. Again, always thinking about long-term value, Rick and Larry stress that it is crucial to leave all the understory intact after the thinning. Although the biggest skidder in the business is ranging through this tract, great pains are taken to ensure that not a single sapling is run over unnecessarily. For his purposes, Larry considers the 635E the ultimate skidding machine – great for long distances, with the flotation to extend the winter season. In late winter, the skidders will also do return trips with brush to fill in the main skid trails with a thick layer of highly effective mat material to further extend the season.
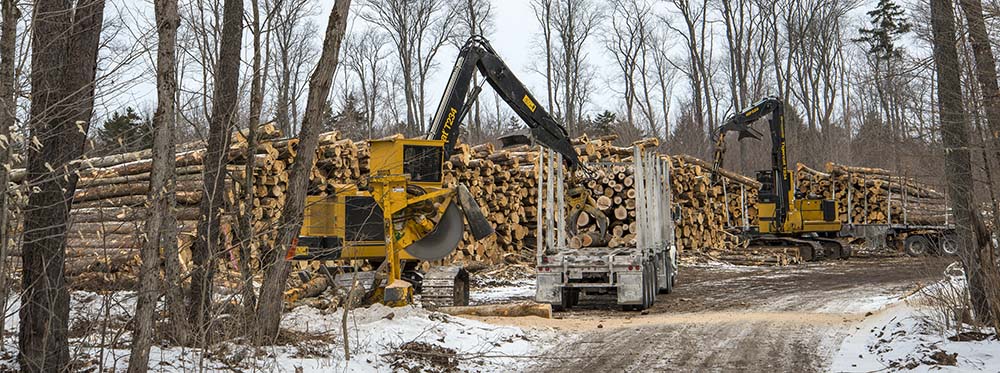
On the hardwood job, T234B loaders equipped with circle saws cut to length and load.
Larry and his wife Theresa have been married 23 years and have three children, Allison, Elaine and Bryce. Although relatively new to the business, Theresa provides key support in the office, managing payroll, stumpage and inventory. “My parents are mostly retired,” explains Larry “and my son Bryce [16] is interested in the business and works part time with us.”
Larry’s mother, Cora Mae has been part of the company for over thirty years. Over the last two years as Cora Mae has decided to semi-retire, the company hired Michelle Delair to take over her responsibilities in the office.
“Kerry Amell has worked with us for over twenty years,” explains Larry. “His dedication to the business and the knowledge he has taken in over the years has made him a valuable asset at the yard and in the woods.” Richards Logging employs ten machine operators, usually two or three in the wood yard, along with two technicians in the shop. The company performs all of its own service work on the machines and the trucks. There are ten truck drivers and two in the office.
Land improvement
Larry recently purchased a 345 ha (850 acre) parcel of timberland near Tupper Lake. The property comes with a lake, a cabin and a bit of history. There has been logging activity in the past and the goal is a land improvement project. Larry will clean up the waste wood that has been left on the ground and market the biomass. Through proper selective harvesting practices, he will be able to harvest some marketable timber and promote new growth, eventually improving the quality of the timber stand.
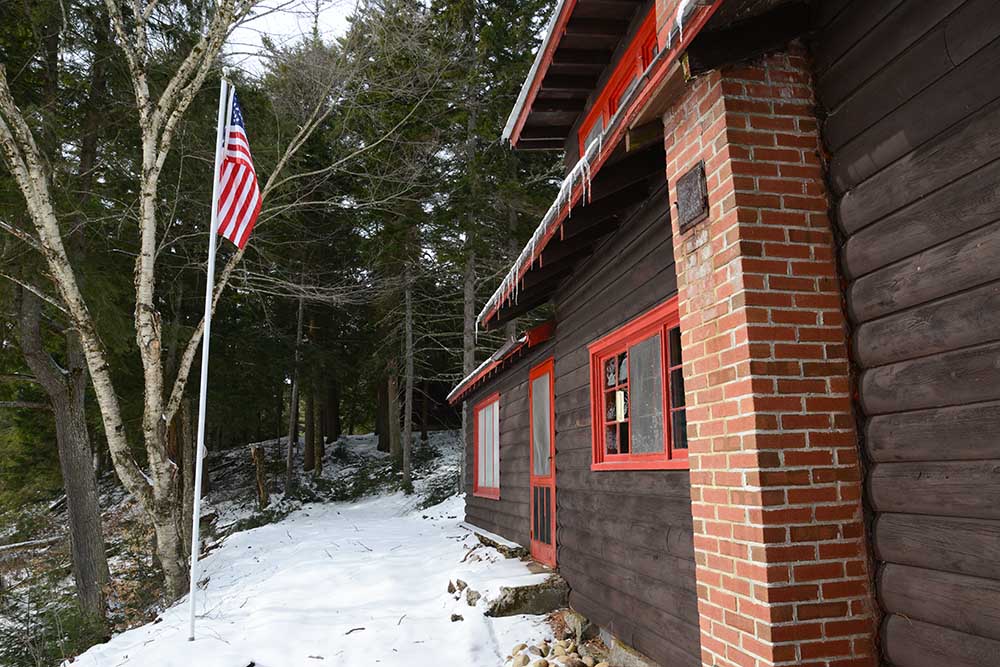
An idyllic lakeside cabin sits on the 345 ha (850 acre) parcel of timberland that will undergo a land improvement treatment.
He plans to perform other site improvements, like cutting recreational trails, improving the road and renovating the cabin that overlooks the lake. “It is good ground that gives us something to do in the spring,” he says. It is one more example of progressive thinking – leveraging the company’s unique skill set to look beyond harvesting timber for additional and innovative ways to diversify and create value.