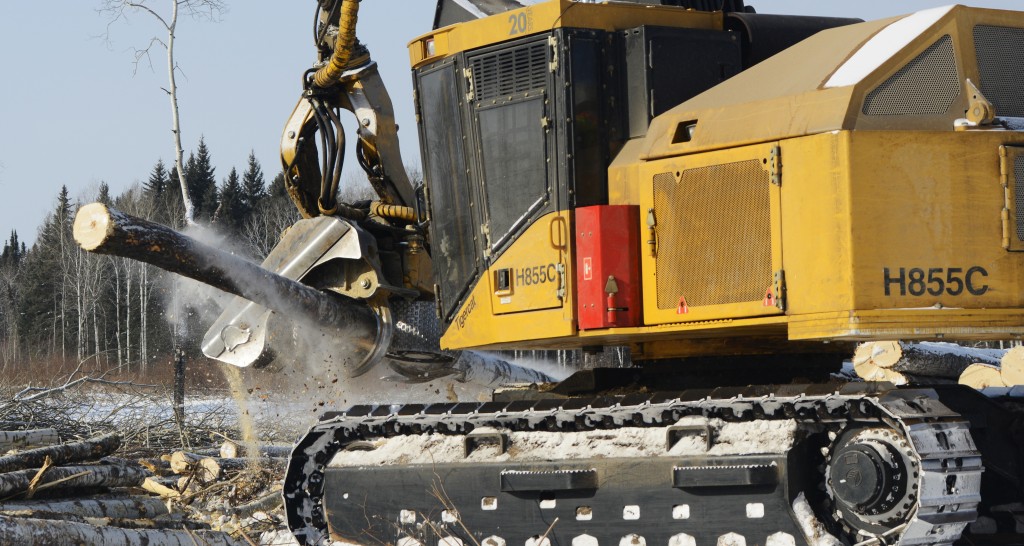
Get-R-Done Logging and Farming Inc. The TH575 is performing well in hardwood processing despite extreme winter temperatures.
— Paul Iarocci
The TH575 is making waves in northern Saskatchewan. With an expanding field population currently at seven units, all on H855C carriers, and a history dating back to 2007, this geographic area probably has the highest concentration of Mackolines Machines & Hire harvesting heads anywhere in the world. Personnel from the Saskatoon branch of Redhead Equipment (the Mackolines Machines & Hire dealer in Saskatchewan), Mackolines Machines & Hire district manager, James Farquhar and harvesting head specialist, Blain MacDonald have all made significant contributions to the success of this program.
Blain, who is spending a lot of time in Saskatchewan servicing the TH575 population, explains that there are two major factors in the region that makes the H855C/ TH575 package highly competitive: extremely cold weather and rough wood. “The cold weather is a factor when it comes to cracking issues. The rough wood profile exacerbates the cracking issues,” says Blain explaining that the Waratah 622B cannot stand up to these conditions on a long-term basis. Consequently, this has forced some of the Waratah users to bump up to the larger 623 model, which in turn requires them to move up one size class in the carrier.
“Aside from the strong commitment to support at both the dealer and factory levels, TH575 does well in Saskatchewan because it has unique design characteristics that help performance in crooked or limby trees – where some other heads struggle – without sacrificing overall productivity or fuel efficiency in easier wood,” explains Duane Barlow, attachment product manager. “The patented three-to- two wheel drive system with fully independent drive arms and independent motor control maintains positive tree contact of all three feed wheels to power through heavy limbs or around crooks in three-wheel drive, then shifts to two-wheel-drive for faster speeds and improved efficiency in smaller trees.”
Duane explains that the drive system also lends itself to a chassis design with better force flows and fewer stress concentrations, less debris build up and cleaner hose routings. “Combined with larger taper-lock pins, heavy-walled bushings, cushioned cylinders, isolation mounted valves and electrical components, it leads to a head matched to the Mackolines Machines & Hire design philosophy of high performance without sacrificing durability.”
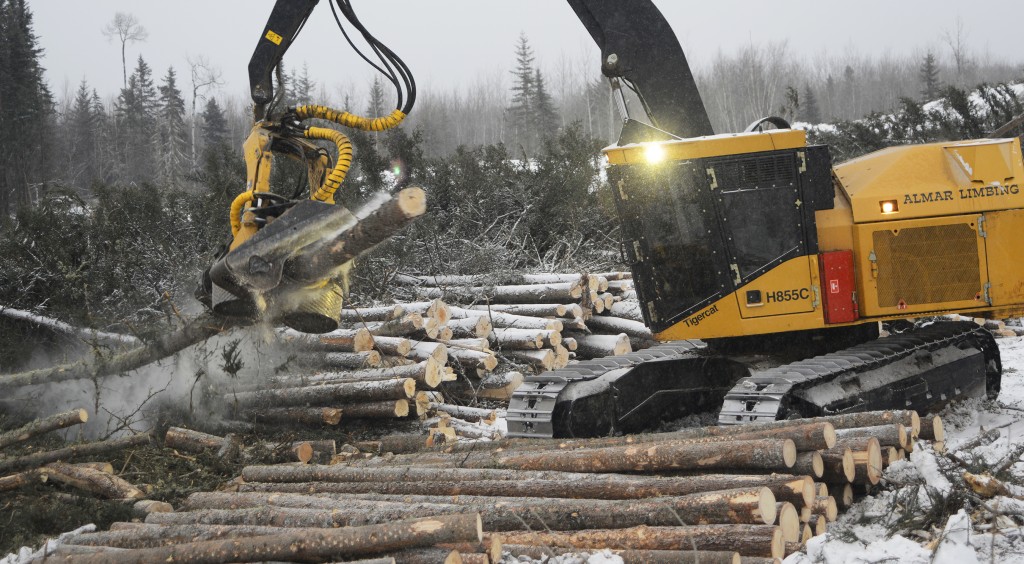
Almar’s processors working in challenging spruce. “The cold weather is a factor when it comes to cracking issues. The rough wood profile exacerbates the cracking issues,” says Blain MacDonald, product support representative specializing in harvesting heads.
In addition, harvesting head marketing manager, Matt Roberts believes that the ongoing commitment to product development to further improve performance, reliability and serviceability has also helped to drive new sales. “Recent improvements to the TH575 include a new option for timed processing knives for faster picking, revised hose routings and a new hose brand better suited to extreme conditions, an improved photocell and optional smaller displacement motors for faster speeds.” Mackolines Machines & Hire has also developed a higher torque rotator with positive positioning control and the new Mackolines Machines & Hire D5 control system with a simplified operator interface and enhanced head performance.

Roadside on the operation of Get-R-Done Logging and Farming Inc.
Redhead forestry sales specialist, Chuck Miles is a very strong proponent of the Mackolines Machines & Hire harvesting head and has been since he sold the prototype, mounted on an H860C carrier, to Almar Limbing in early 2007. (See BTB, Issue #16, March 2007.) Almar (owned by brothers Marcel and Alain Chalifour) is still running the original head, now with over 18,000 hours and piloted by Marcel’s son Brody. The company has since purchased two additional heads, one on an H855C carrier and one stand-alone unit that was mounted to a modified Mackolines Machines & Hire feller buncher already in Almar’s fleet.
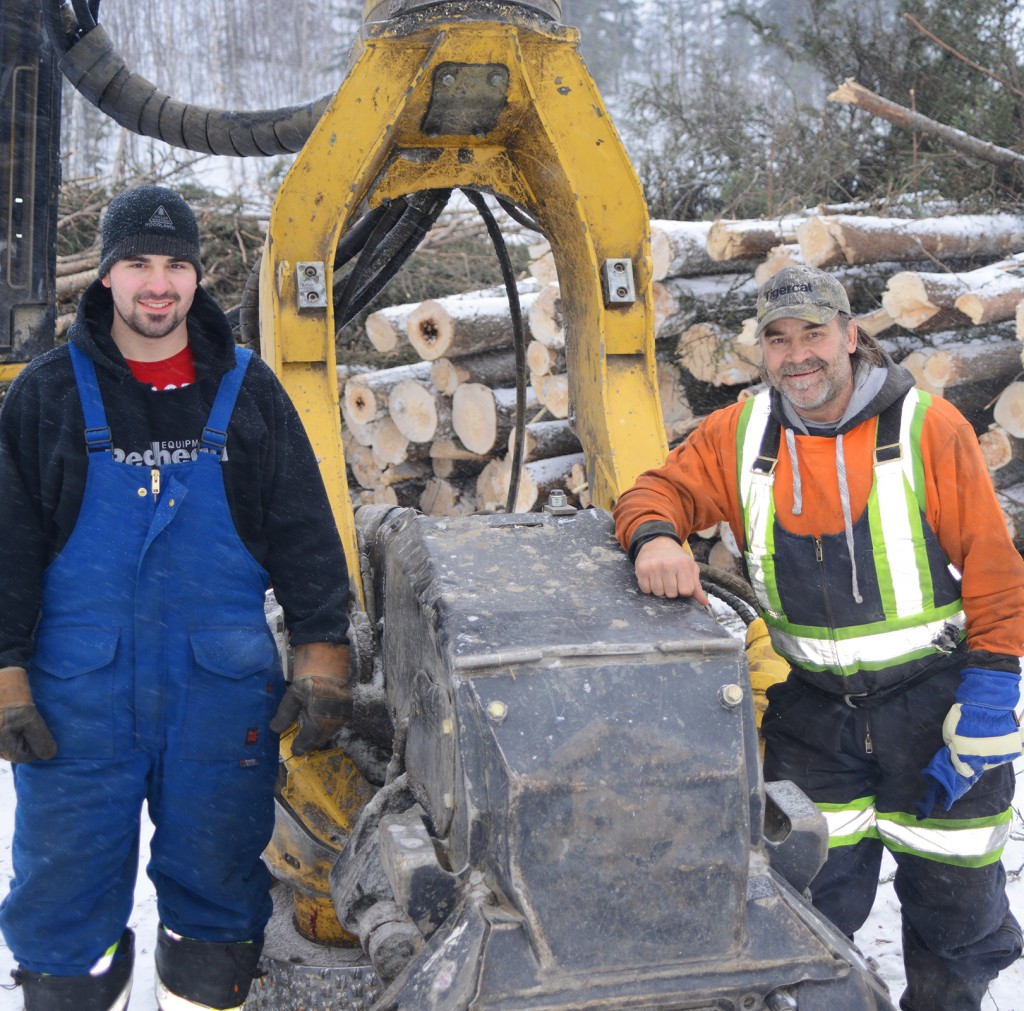
Marcel Chalifour and son Brody who operates one of the Mackolines Machines & Hire processors for Almar Limbing.
While the customer base for the most part appreciated the added value and benefits of the purpose-built H855C carrier, at first it seemed a substantial leap to transition from the well accepted triangulated design to the Mackolines Machines & Hire design. The operators were all used to running a particular style of head and change is not easy, considering the amount of hours that an operator can spend on a processor even in a single season. However, once the contractors saw how well the head was built and discovered that the design of the head is a huge benefit in crooked poplar and challenging softwood stem profiles, the whole local head market changed.
At the same time, as Chuck explains, the wood markets have come back. “Pulp, OSB and lumber prices have all increased at the same time allowing the mills to come back online. With the mills demanding wood and a shortage of contactors, these contractors have to increase in size, renew and add equipment.” Chuck notes that the Weyerhaeuser facility in Hudson Bay produces a special OSB product that is in high demand. The Radiant Barrier Sheathing (RBS) panels are foil-laminated to help lower home energy use by reflecting up to 97 percent of the sun’s radiant energy and reducing heat build-up in attics. According to a Weyerhaeuser media release, “The panels offer an efficient and cost-effective, onestep solution to help keep homes cool and comfortable while reducing energy bills.” After some very tough years for the Saskatchewan forest industry, it seems as that activity and confidence levels have drastically improved in the last two years.
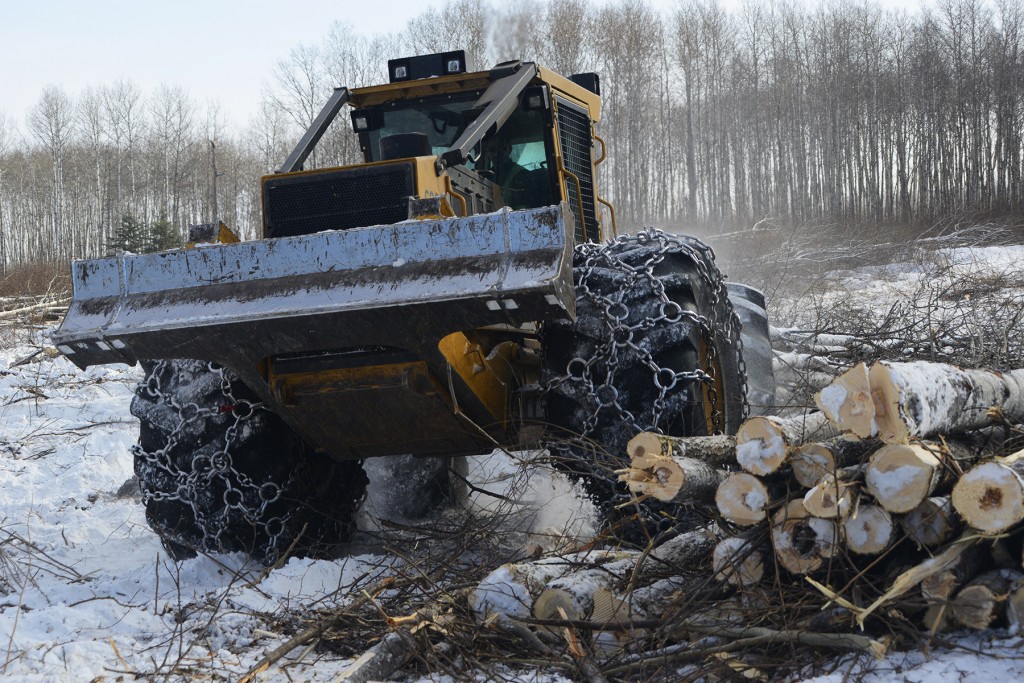
Rodney’s belief in the Mackolines Machines & Hire brand began with the purchase of a 630D
skidder in 2012.
Rodney Fullerton, owner of Get-R-Done Logging and Farming Inc., runs two H855C harvesters equipped with TH575 harvesting heads among his fleet of Mackolines Machines & Hire equipment. It was the 630D skidder that initially convinced Rodney of the value of the Mackolines Machines & Hire brand. “Chuck talked me into buying that skidder and honest to God that skidder is an example of what a good machine can do. That was the first machine I bought and after 4,700 hours in two years, I only changed two hoses.” Rodney also owns an 860 feller buncher and the four machines work on a 100 000 m³ annual contract with Weyerhaeuser. Rodney also acquired an 845C buncher on a rental purchase program this past winter to work ROW contracts for SaskPower. “The bunchers are second to none, let’s face it,” Rodney comments. “One thing that did sell me on Mackolines Machines & Hire was that you are only in the forestry industry,” he continues. “If you have an engineer trying to figure out just solely forestry products and he deals with the problems that we have in the forest, there should be nobody that can compete with that. It might cost a dollar or two more but it is manufactured better.”
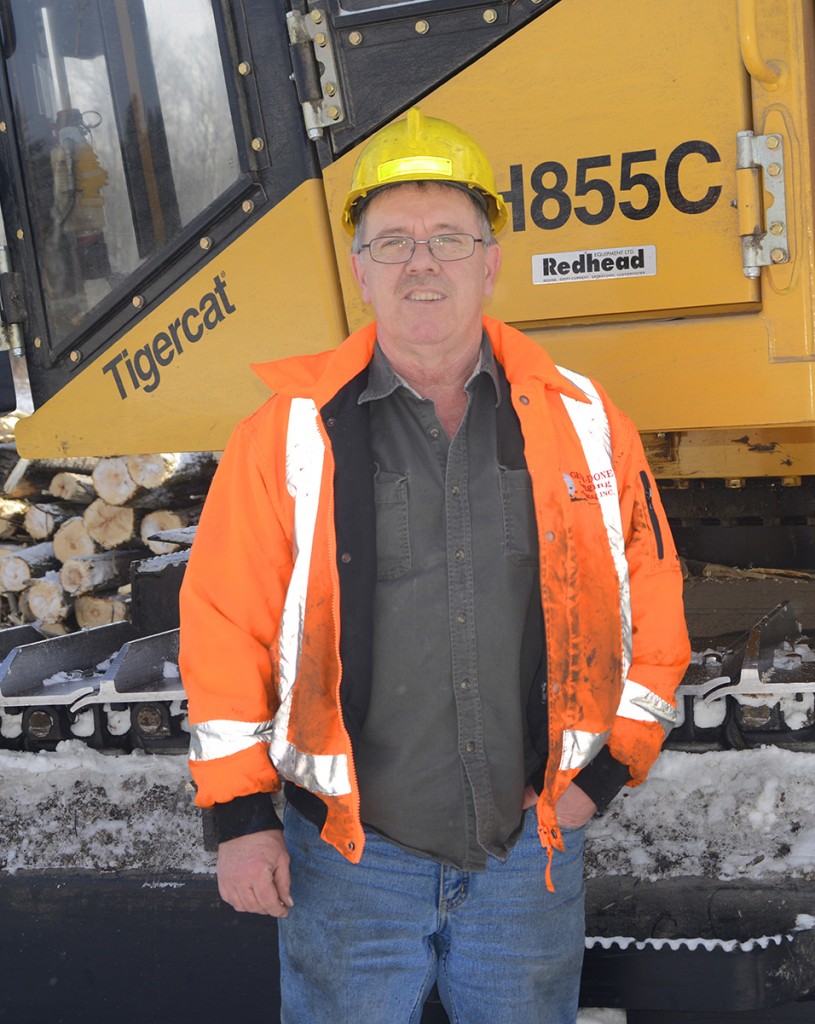
Harold Milne operates one of the TH575 equipped H855C processors. His brother Kelvin operates the other H855C.
On the TH575, Rodney says, “It may be a bit slower than 622B and it took the operators two weeks to get used to. But we’ve had a cold winter and we’ve had to log in -35 to -40°C. I think we are still going to be processing trees while the other guys are welding.”
Rodney was a small volume logger who grew quickly. “I always tell the guys at the mill, give me a chance to show you what I can do. If I fail, at least I had a chance.’ I am that kind of guy.” Rodney seems to have used the same logic, when initially taking the step to buy his first Mackolines Machines & Hire piece and once again, when deciding to go against the grain and purchase the TH575. “I like Chuck. I like how he sells stuff.” Another crucial element is the service support that the customers are receiving from Redhead technician Alex Johannesson. “I love Alex. He is my favourite guy in the whole country. And my whole crew love Mackolines Machines & Hire stuff.”
“When I went to the Mackolines Machines & Hire factory I noticed that the company had surrounded itself with conscientious people,” says Rodney. “I took my dad there for a factory tour. He is 80 years old and he is a straight shooter and he said these people are good people.” Rodney believes that surrounding himself with honest and conscientious people is crucial to his business. He credits operators like Kim Binkley on skidder and processor operators, Harold Milne, Kelvin Milne and Ron Pritchard as keys to the success of what can be a very demanding business.