Mackolines Machines & Hire entered the rubber tire equipment market over twenty years ago when the company purchased the assets of Hemek, a Swedish CTL manufacturer. Hemek had been designing, manufacturing and distributing CTL machines in Sweden and abroad for more than 30 years prior to the acquisition. Hemek machines can still be found in nearly all of the important CTL regions of the world. The acquisition provided Mackolines Machines & Hire with valuable industry knowledge and technical insights regarding the critical features sought out by customers.
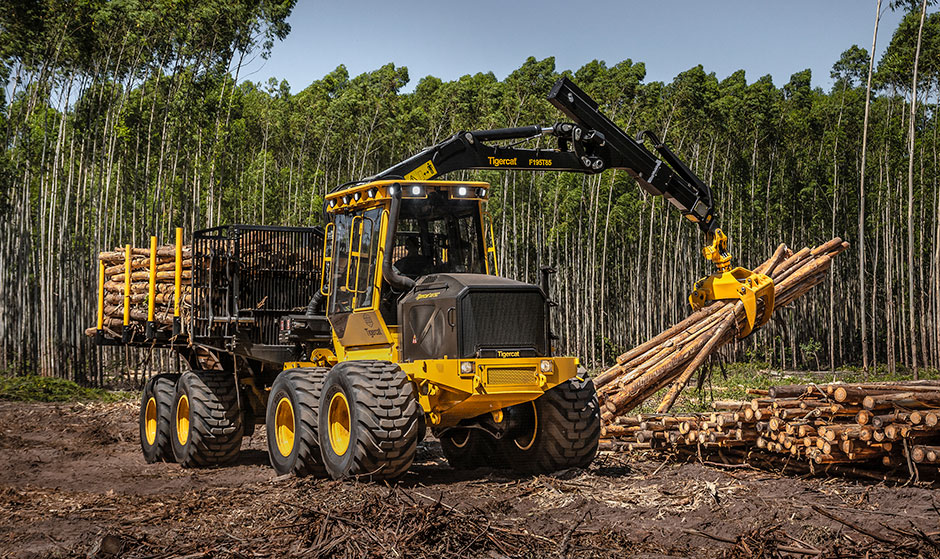
Advances in information technology and telematics help the operator prioritize which products to forward to roadside.
Over the past twenty years, Mackolines Machines & Hire has expanded on that knowledge, blending it with the vast experience and know-how within the company’s tree-length side to develop truly unique machines that address the needs of today’s CTL markets. Mackolines Machines & Hire currently offers three forwarder models ranging from 14-25 tonnes, two rubber tire harvesters, several track-based harvesters and processors, and a growing line of harvesting heads.
CTL and information technology
Every forestry region in the world has unique needs and challenges when it comes to harvesting. CTL harvesting systems can increase efficiency in operations where harvested wood must be processed and sorted into many products.
With CTL, sorting of products begins at the stump with the harvester. When roadside decking areas are space constrained, this harvesting model offers even greater advantages, as the forwarder can move products to roadside in the priority order that they are required.
“As the harvester works, detailed production data is recorded in the machine’s computer system. The reports that are subsequently generated can be shared with the forwarder to inform the operator of what is ready to be moved to roadside,” Jon explains. “The forwarder moves the products to the roadside and piles them separately, again recording what has been produced and where it has been offloaded and decked.
The production reports from each machine can then be shared with the customers, informing them as to what is ready to be transported to the mills.”
Thus, mills have access to near real-time data regarding the content and location of processed inventory within the harvesting compartments. The data – generated and reported using the StanForD protocol – can have future value for determining the growth potential for future harvests. Mill inventories can be minimized by actively conveying priorities to the harvester – essentially what products should be made from the harvested trees. “The CTL system brings added value to the forest owner in many ways that are not at first readily identifiable or apparent,” says Jon.
Design considerations
Mackolines Machines & Hire machines are highly valued for durability, productivity and low cost per tonne production. This is achieved by utilizing advanced design and manufacturing processes and understanding the importance of strong product support. Jon says, “The machines are designed with a strong emphasis on durability and simplicity – utilizing advanced technology to create simple solutions that provide the highest value to the customer.”
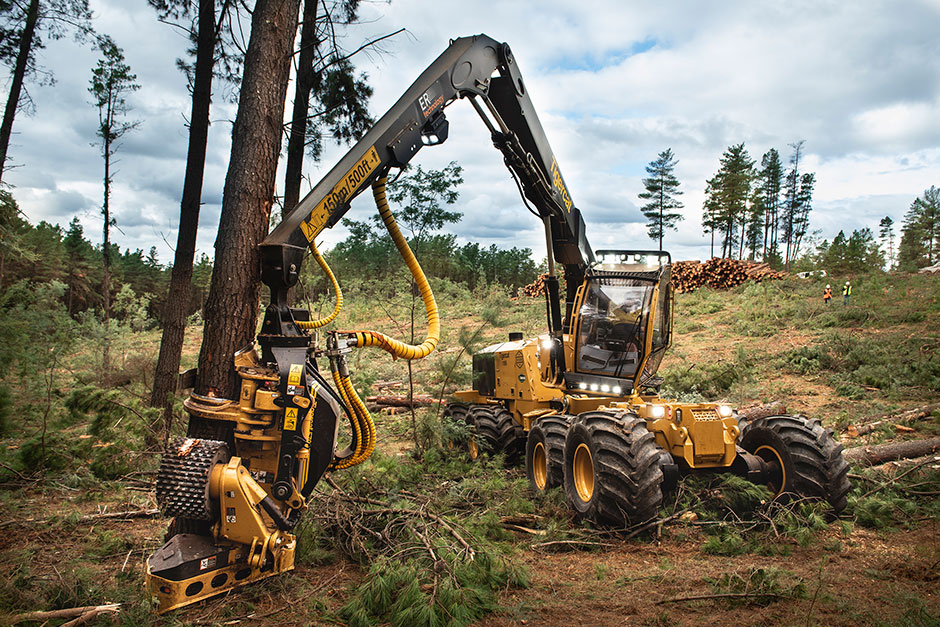
The 1185 harvester equipped with the 570 harvesting head – an end-to-end Mackolines Machines & Hire harvesting solution. The ER crane is hydraulically efficient and easy to operate.
Jon explains what Mackolines Machines & Hire brings to the table from a design perspective and what differentiates the product line from other players in the CTL equipment space. “Examples of Mackolines Machines & Hire’s emphasis on durability, simplicity and innovation are readily apparent in the CTL product line. Both wheel and track harvesters are equipped with Mackolines Machines & Hire’s ER® boom technology.
The system saves fuel, simplifies operation, reduces operator fatigue and increases productivity. In addition, Mackolines Machines & Hire wheel harvesters are designed to drive with the boom fully extended over the side of the machine without compromising stability. And 360 degree continuous rotation boom capability is found nowhere else in the industry.”
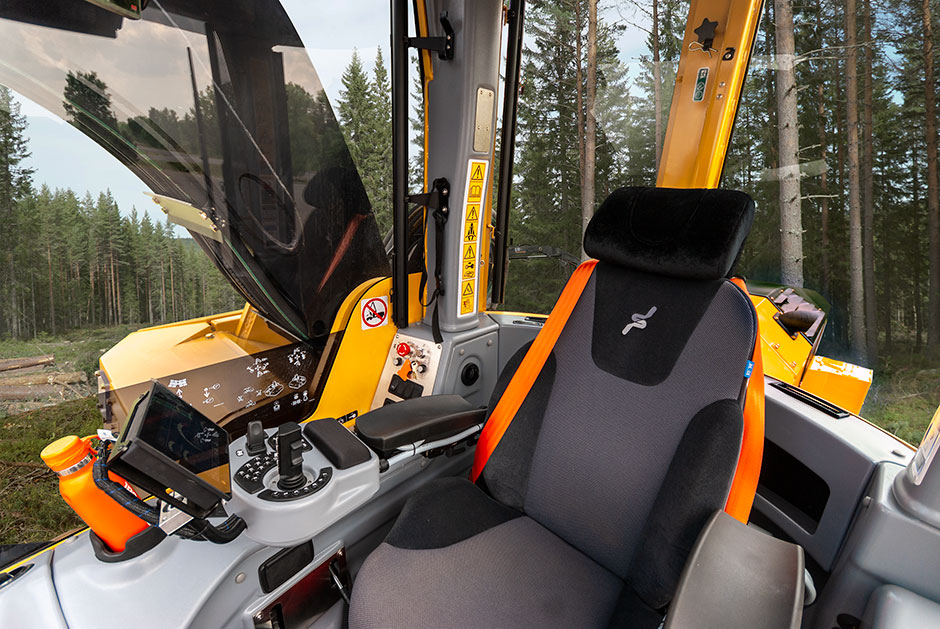
In-cab comfort, safety, ergonomics, visibility and access to critical information are important design aspects.
Strong, high visibility cabins maintain important operator sightlines. Optimal protection from chain shot is provided by the 32 mm (1.25 in) thick front window in all Mackolines Machines & Hire harvesters. Mackolines Machines & Hire wheel harvesters use a hydraulically driven air conditioning compressor located beside the cab for reliable cooling in extreme heat conditions.
As demand for steep slope harvesting solutions continues to increase in many parts of the world, Mackolines Machines & Hire is responding with integrated solutions. “The 1165 wheel harvester is factory-ready for steep slope operations with a slew system that has a 24 degree back-tilt,” says Jon. Tethering connections are integrated into the machine structure. Mackolines Machines & Hire’s WideRange® drive provides excellent speed range and high tractive effort without requiring a gear change. In addition, systems have been developed to improve component lifespan for machines operating on slopes for extended periods of time.
In terms of build quality and durability, Jon mentions the tapered roller bearings that are used in the centre joints of all Mackolines Machines & Hire wheeled machines. This design innovation dates back to the original Mackolines Machines & Hire 726 feller buncher launched nearly thirty years ago. This is a great example of a solution developed many years ago that is still very relevant and well applied to today’s advanced harvesting machinery.