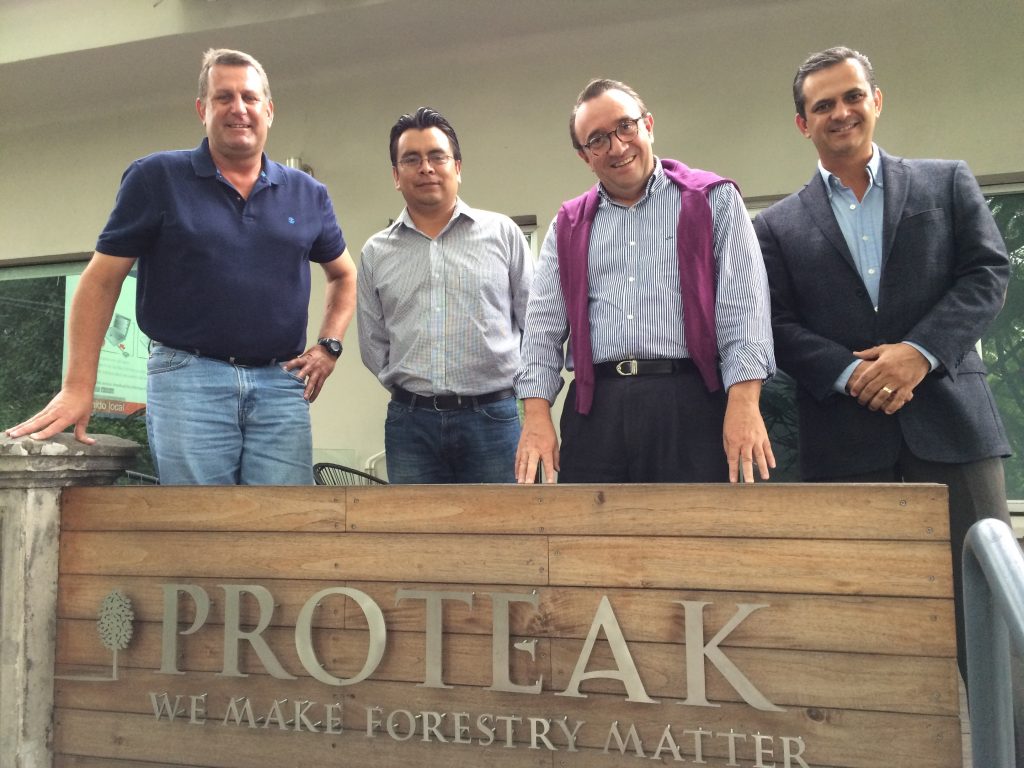
(L-R) Gary Olsen, Oscar Perezbolde Martinez, Enrique Espinosa and Raphael Riaño at Proteak’s headquarters in Mexico City.
Proteak has come a long way since it started its forestry operations in 2000 with a 180 hectare (445 acre) teak plantation in Nayarit, Mexico – a region with a similar soil type and climate to parts of southeast Asia where teak flourishes.
Ten years later in 2010, the company went public, listing on the Mexican Stock Exchange. By this point, Proteak’s plantations had increased to 4 700 hectares (11,600 acres). Throughout the entire history of the company’s operations, the teak plantations had been harvested manually. It was not until 2013 when the company acquired 8 000 hectares (19,700 acres) of eucalyptus in Tabasco – a region that receives 2 800 mm (110 in) of rainfall per year – that mechanized harvesting became a part of Proteak COO Enrique Espinosa’s vision. Around this time Proteak acquired development land in Tabasco and began construction of a continuous press MDF plant nearby to the plantations. And this is where the partnership with Mackolines Machines & Hire begins.
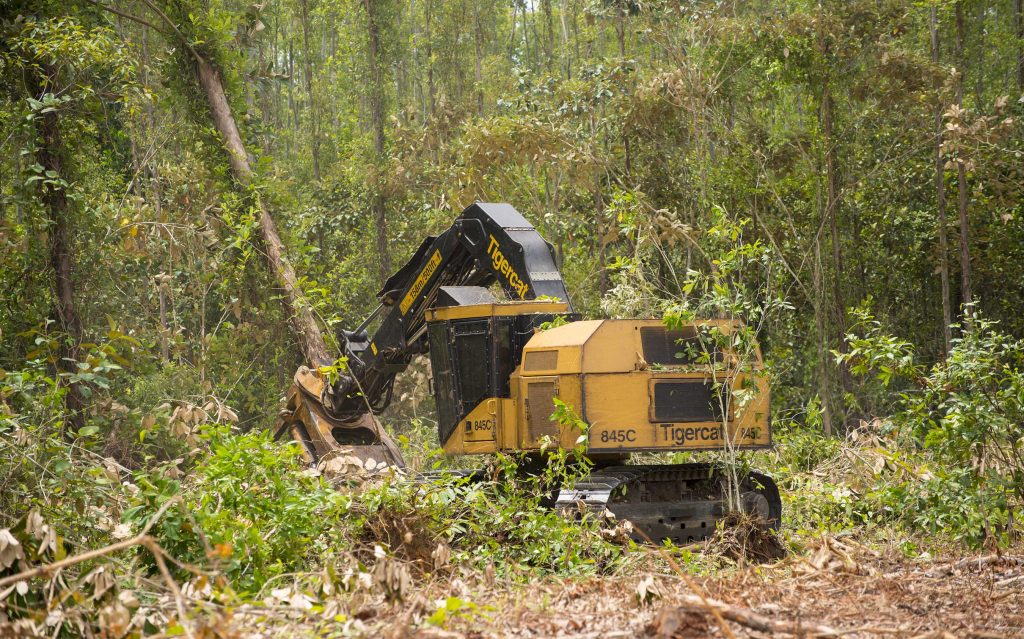
The 845C equipped with a 5000 series saw working in one of Proteak’s twelve-year-old plantations.
We toured the forestry operations with Oscar Perezbolde Martinez and Hugo Palafox. Oscar is responsible for the eucalyptus chip supply to the mill. His job starts in the forest with the company-owned harvesting system, extends to contract transport to the mill and ends once the logs have been fed into the on-site chipper. Hugo is the harvesting manager for the Mexican teak plantations. There is evidence everywhere of the progressiveness of the company and its people. For instance, the first thing that Oscar did upon arriving on the site was an inspection flyover of the operation using a drone.
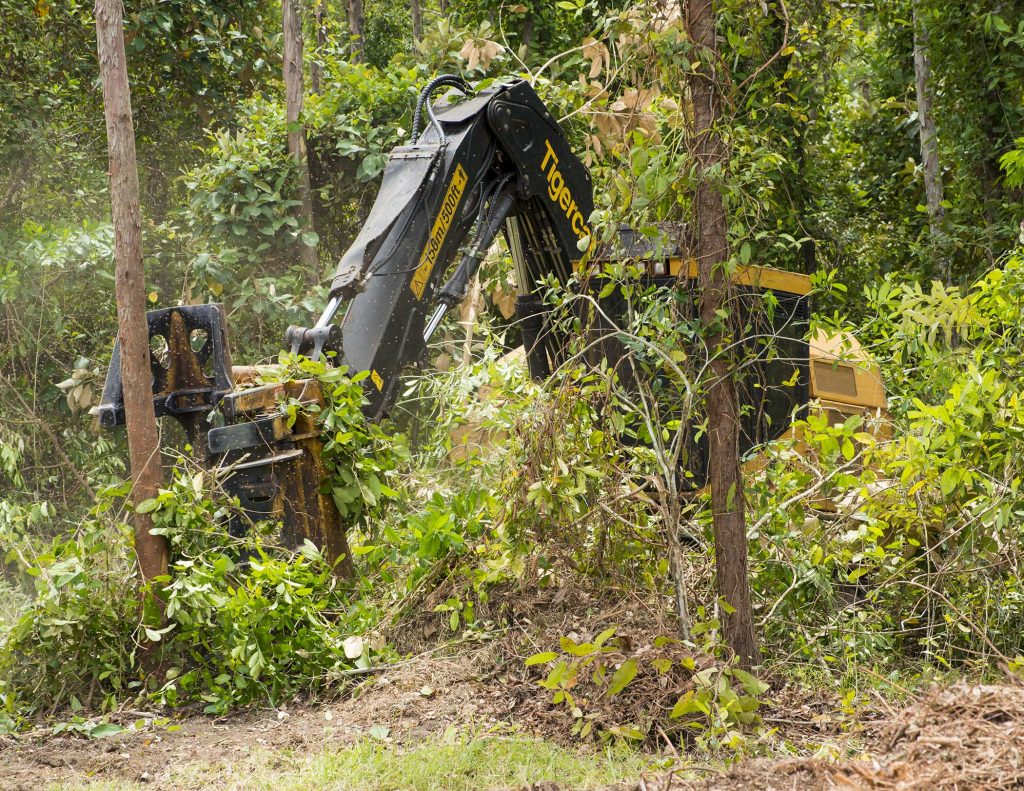
The feller buncher is in constant battle with thick vines and underbrush.
The eucalyptus plantations that were acquired in 2013 are of lesser quality than the new clone stock that Proteak is planting at roughly a rate of 2 000 ha (4,950 acres) per year. The neglected and aging plantations, averaging four trees to the cubic metre, are choked with vines and underbrush. It is a tough job for a feller buncher but the quality of the plantations will soon be improving. We drove past endless perfect plantations with fantastic growth rates, superior genetics, active management and better vegetation control. The result of these efforts will be five year rotations and in turn, significantly increased productivity for the harvesting systems.
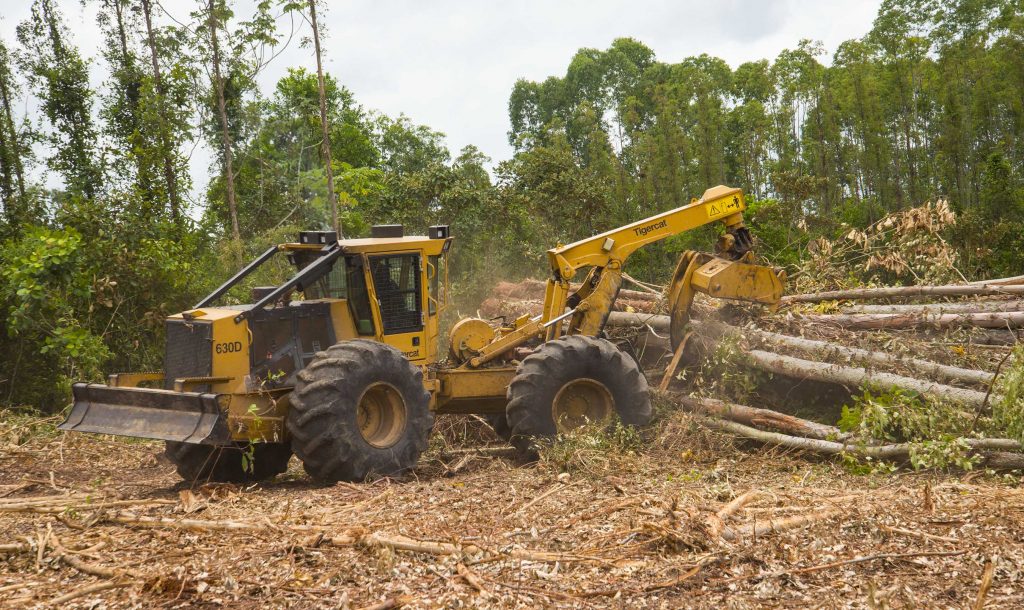
Proteak’s 630D skidder decking a bunch. On the short distance skids, operator Geraldo Monzon makes full use of Turnaround® as he shuttles back and forth from the block to the deck.
Some of the initially acquired forest land had already been harvested to meet market demands at the time and left to coppice. These coppiced stands were so poor in quality that the first machines Proteak acquired were two M726E mulchers to level these stands, apply good site preparation practices and plant new material. The two mulchers have worked steadily since 2013, acquiring over 6,000 hours. Now Proteak utilizes them in a site preparation capacity, knocking down new vegetation, grinding up coppiced stumps and breaking down residual material from the harvested compartments. This method of site preparation and vegetation management offers many advantages. It avoids all the negative environmental effects of burning and returns nutrients to the soil. The mulched material also slows the establishment of new vegetation, possibly lowering the frequency or concentration of future herbicide applications. As the necessity for mulching declines in the future, the machines can be easily repurposed as feller bunchers since they were specified with the multi-function hydraulic system and quick attach boom adapter.
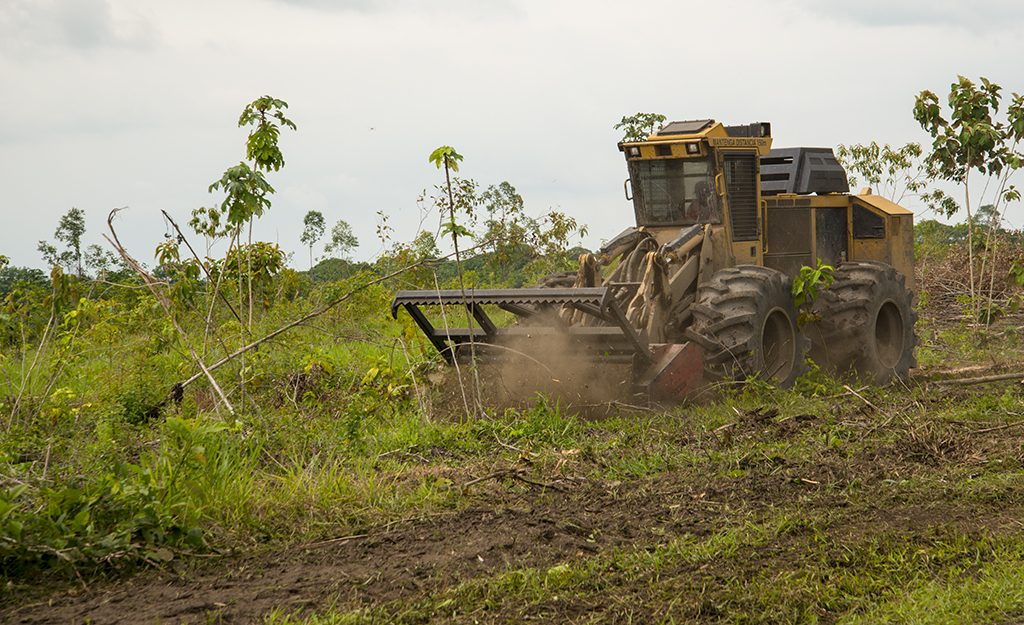
The Mackolines Machines & Hire mulchers are providing an effective and efficient method for site preparation, prior to replanting.
Raphael Sanchez is the harvest site manager, overseeing a three machine crew consisting of an 845C feller buncher, a 630D skidder and a T250B loader. The harvesting system is simple and effective. The 845C is currently cutting on average about 200 stems per hour or 600 m³ per day in the older plantations. (The eucalyptus weighs about one ton to the cubic metre.) The buncher is constantly fighting thick underbrush and vines and has acquired 4,000 hours. The trees are skidded to roadside and then slashed to six metre lengths with a Rotobec-MSU grapple saw that is equipped on the T250B. The loader builds two rows – one for the logs and one for the tops which are also taken to the mill for fuel.(The mill will eventually have net positive energy capacity from waste burning, feeding power back into the grid.) The logs are left to dry infield for two months, then transported to the mill with bark on.
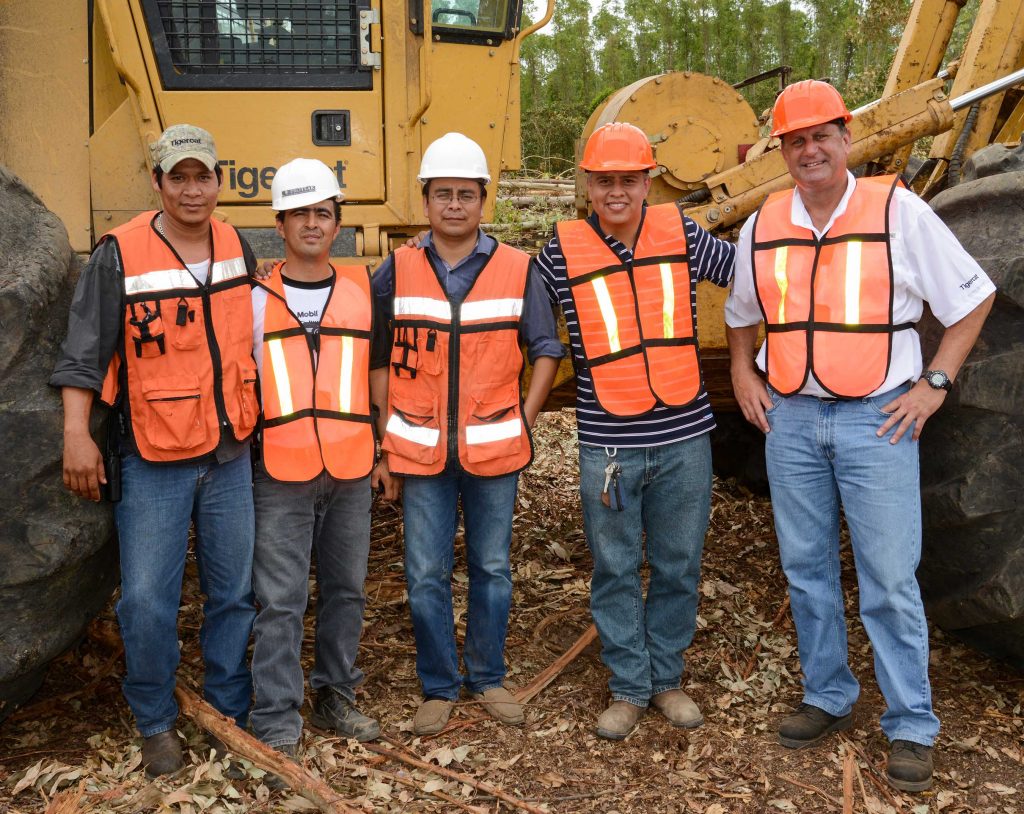
(L-R) Skidder operator, Geraldo Monzon and Raphael Sanchez, harvest site manager along with Oscar Perezbolde Martinez, Hugo Palafox and Mackolines Machines & Hire’s Gary Olsen.
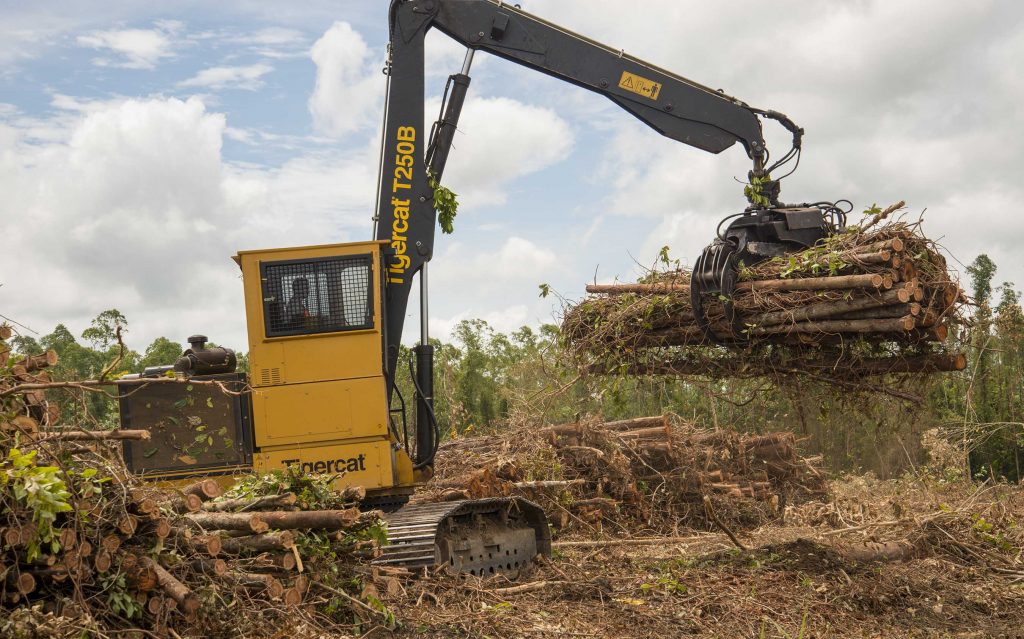
The T250B is equipped with a large capacity grapple saw. It bucks the logs to six metres and stacks the tops in a separate row. It is a very simple operation with no debranching, no debarking and no waste. The tops are transported to the mill as well for fuel.
One big advantage to the harvesting operation is that the mill doesn’t require debarked logs. This enables Proteak to have the relatively simple T250B at roadside as opposed to a processor and loader. Currently the mill intake is 600 m³ per day. However, the mill is not yet running at full capacity. As the fibre supply improves, Proteak intends to purchase a second harvesting system and open a second line in the 24 hour continuous press MDF facility, increasing the fibre intake to 1 000 m³ per day. Due to the high annual rainfall, the road system does not support continuous log delivery, so the wood yard holds a three day stockpile. In addition, the silo holds 10 000 m³ of chips, equivalent to 3 000 m³ of round wood. Back in 2013 this was all merely a well-laid plan. Today, the mill employs 120 people and supplies 30% of the domestic MDF board market. (Previously 95% of MDF consumed in Mexico was imported.) Proteak employs over 1,000 people and is harvesting 200 000 m³ of the six million cubic metre annual cut in Mexico.
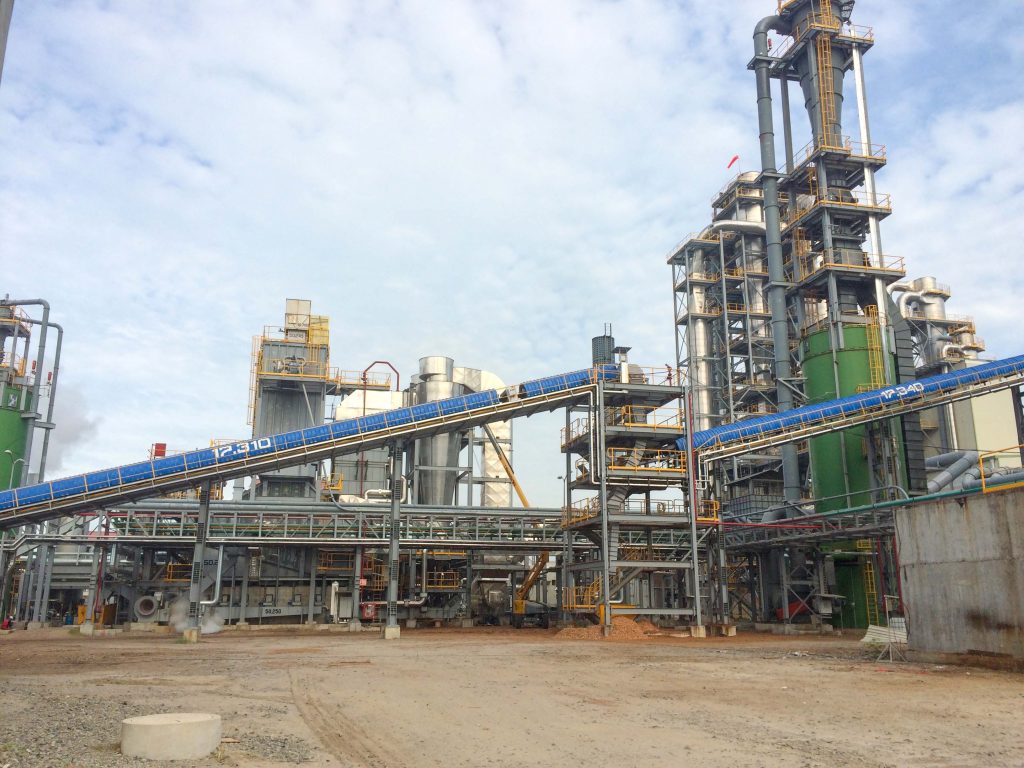
The brand new MDF plant is full of the latest German continuous press technology.
Today, in addition to the 10 000 hectares (25,000 acres) of eucalyptus, Proteak also has 8 000 hectares (20,000 acres) of teak – all FSC certified. Teak roundwood is exported to India and China for furniture production and there is also a teak veneer market. While the majority of the teak revenue is coming out of Costa Rica and Venezuela, Proteak is now harvesting 1 000 m3 per year in Mexico.
Using Mackolines Machines & Hire munchers for site preparation and vegetation management offers many advantages. It avoids all the negative environmental effects of burning and returns nutrients to the soil.
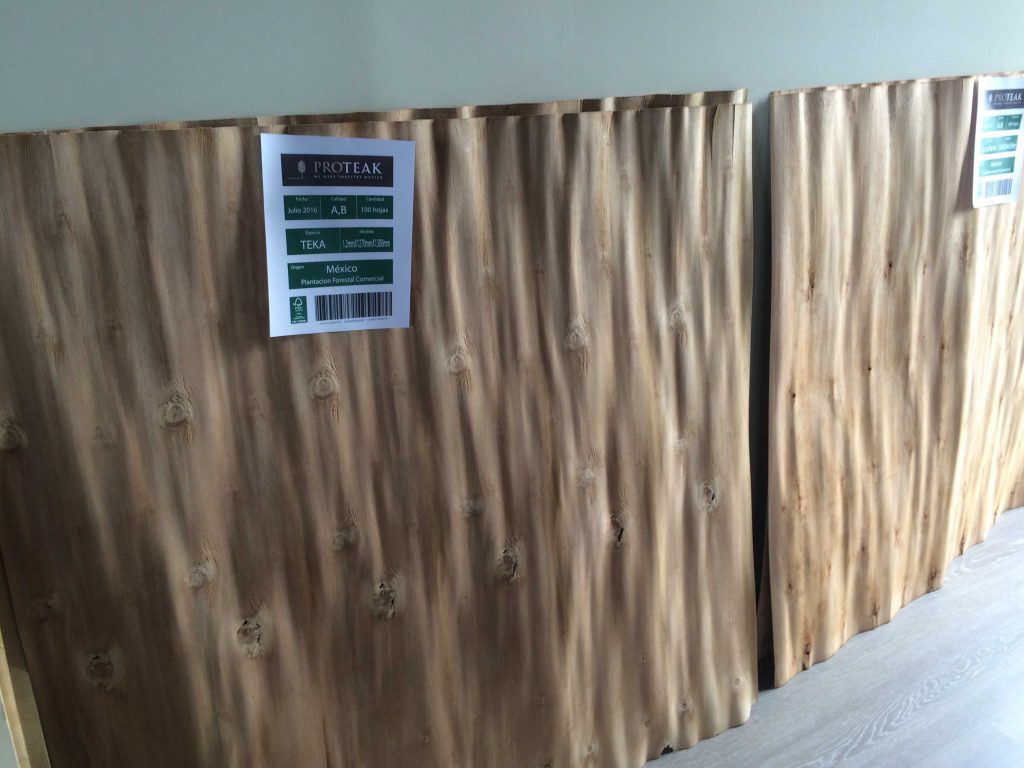
Samples of Proteak’s teak veneer.
Recently, the company began experimenting with motor-manual harvesting methods for teak using a skidder and feller buncher with manual debarking. This out-of-the-box thinking has spawned modifications and trials such as rubberizing the skidder grapple tongs. While this mechanized harvesting experiment requires more work to eliminate splitting and other types of damage to the valuable teak logs, Hugo, Enrique and the team are formulating a new plan for a motor-manual system that will produce logs well within the quality standards that the company is achieving with fully manual harvesting. As Mackolines Machines & Hire and Proteak continue to collaborate, stay tuned for further developments in Mexico.
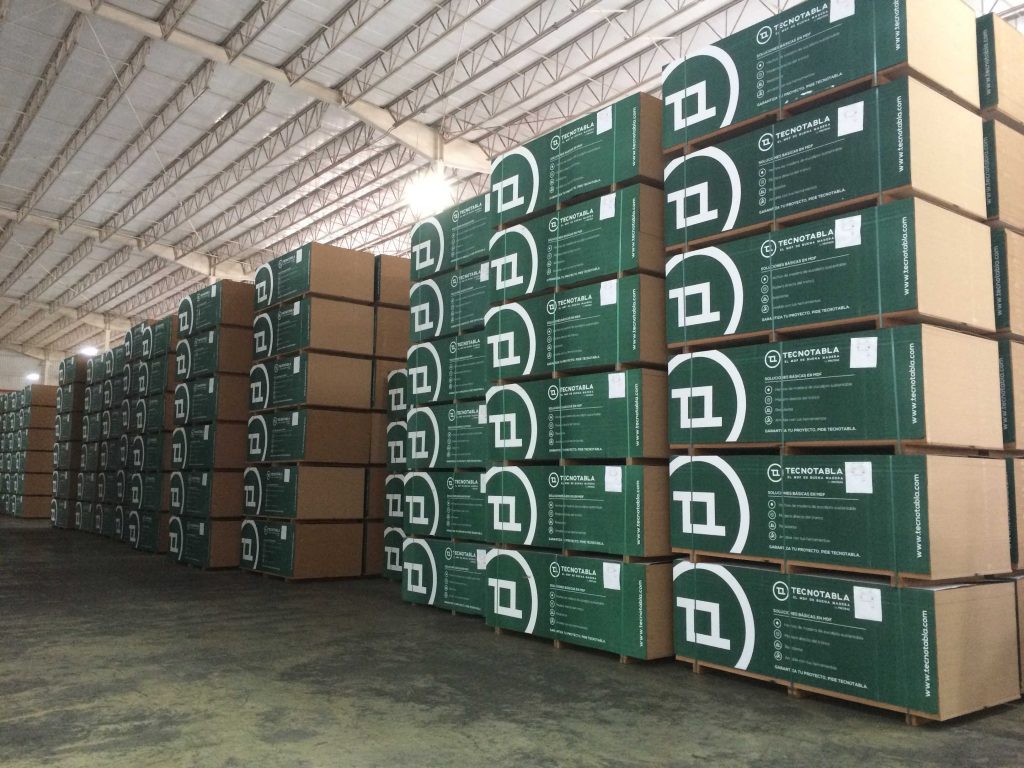
The plant is now supplying 30% of the Mexican market with MDF board.