– Bre Elbourn
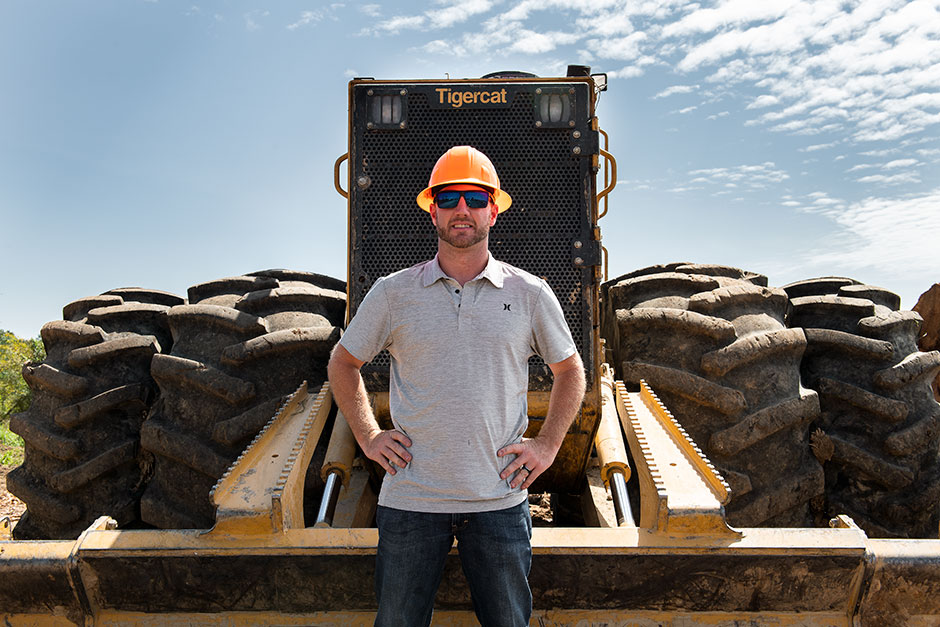
Chris Gibson, Chris Gibson Logging LLC.
The prototype 632H skidder can be found on the job site of Chris Gibson Logging LLC. The machine is tucked in the southeastern part of Oklahoma, working near Broken Bow, in McCurtain County. Owner Chris Gibson is a progressive logger who strives to stay ahead of the pack. With only a single skidder on the job, productivity and uptime are of the utmost importance.
Over the years as a Mackolines Machines & Hire customer, Chris has forged a great working relationship with the Mackolines Machines & Hire skidder team and has had some involvement both in the initial development of the 632 model and in the redesign of the H-series skidder operator’s cab. In fact, it was after some time spent at Gibson’s logging operations that Jeremy Piercy, skidder product manager, started planning the design of the 632 platform. A few years later, Chris purchased the prototype 632H, the very first H-series skidder ever built.
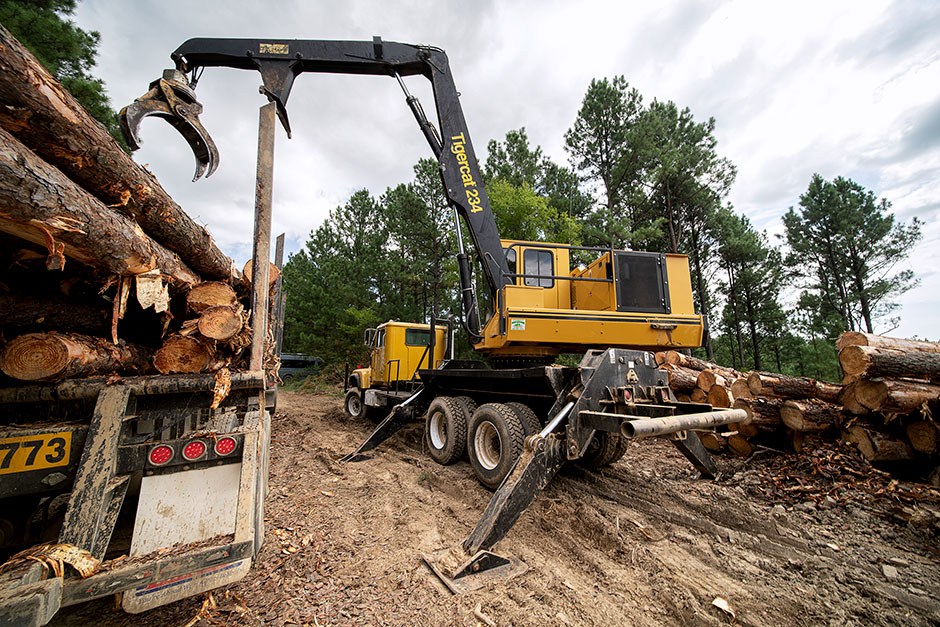
Loaders are mounted on trucks for quick and easy mobility.
McCurtain County, Oklahoma
Oklahoma is defined by more than 12 million acres (4,8 million hectares) of forestland, with its timber industry located in eighteen eastern counties. McCurtain County itself is surrounded by pine forests and is abundant in wildlife. It is no surprise that agriculture and forestry dominate the economy in the county. The Three Rivers Wildlife Management Area is just north of Broken Bow, with 450,000 acres (182 000 hectares) of land owned by Weyerhaeuser. “We’re 100% clear-cutting loblolly pine for Weyerhaeuser,” Chris tells us.
The city of Broken Bow sits between the Ouachita Mountains and the Red River basin. The basin consists of flat and fertile agricultural land. Chris explains that the 632H is primarily working on flat ground, “It’s about half soft and gets a little rockier when you move into the hilly terrain.”
Mackolines Machines & Hire dealer Smith Equipment serves the area. Gibson’s sales specialist is Jeff Reynolds. “Support is great. I mean, hands down they treat me very, very well,” Gibson proclaims.
THERE IS A LOT MORE UPTIME WHEN WE’RE WORKING WITH
THE MACHINE AND NOT ON THEM.
– Chris Gibson, owner of Chris Gibson Logging LLC
Operations
Chris Gibson is a fourth-generation logger. He owns Chris Gibson Logging LLC, Chris Gibson Trucking LLC and Chris Gibson Truck Repair LLC. Having come from a long line of loggers, Chris has the backing of generations of knowledge and applies this to maximizing efficiency in his operations. He has sixteen employees working
in the forest, with the team split between three logging crews. Chris’ wife Jasmine manages two office administration staff. “There are a total of three that work in the office, my wife and two other ladies. My wife manages my whole office. Separately, there are three mechanics that work in my shop that take care of my trucks and the equipment,” Chris explains. Chris Gibson Trucking LLC is made up of seventeen employees and the company does all of the hauling and repairs, giving Chris full control over operations from the stump to the mill.
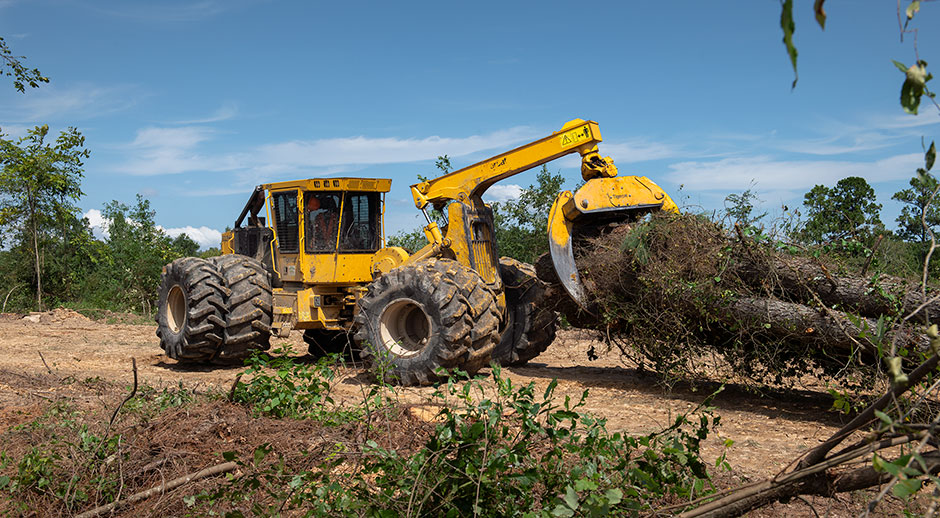
The H-series machines have made it easier to upkeep common wear areas. Chris Gibson appreciates the interchangeable grapple tips.
Developing the 632
When the LX830 model advanced to the D-series, Chris’ dealer Smith Equipment brought him to tour the Mackolines Machines & Hire plants in southern Ontario. Chris explains that he wanted “to make sure that the LX830D was what I wanted before I bought it.” He had just bought his first John Deere 948L skidder and when the tour group made its way over to the skidder plant at Savage Drive in Cambridge, Jeremy and Chris got talking about his new machine. The 630 was Mackolines Machines & Hire’s highest capacity four-wheel skidder at that time, and Jeremy was eager to see how the 630E compared to the biggest of the competitive models in a high production Oklahoma application.
THE 632H WILL GET A BIGGER DRAG THAN OUR PREVIOUS MACHINE.
– Chris Lacefield, 632H skidder operator, Chris Gibson Logging LLC
Jeremy and Shawn Pette, vice president, tree length systems, headed down to Oklahoma to demo a 630E skidder on Gibson’s operations. The visit highlighted to Jeremy that Chris had a unique way of looking at a logging operation, and that he was the kind of logger that was successfully pushing the limits. This got Jeremy thinking about what Mackolines Machines & Hire could do to help loggers like Chris continue to become more efficient and ultimately more successful in the woods. The next logical step in the skidder offering was to create a 630 sized machine that was capable of moving more wood, more efficiently, and without compromising reliability.
The visit with Chris helped guide the Mackolines Machines & Hire drivetrain and skidder engineering groups in creating a higher capacity rear axle, new hydraulic systems and ultimately the 632E that was launched at Demo International 2016 in BC.
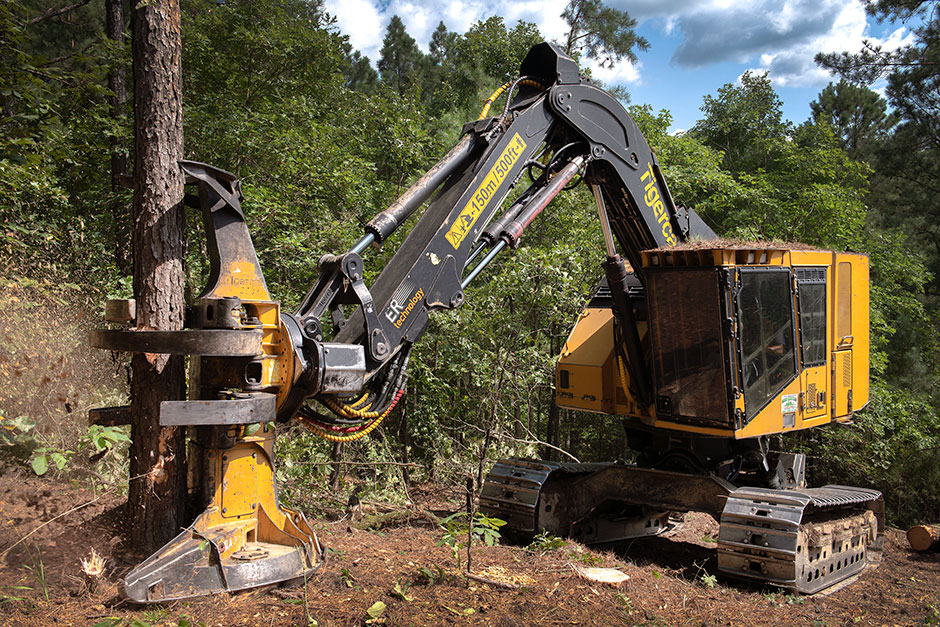
Chris toured the Mackolines Machines & Hire factories before deciding to purchase the LX830D model.
Fast forward a few years from the launch of the 632E. It became clear that the next area that needed attention on the skidder product line was the operator’s cab. During the early design stages, Chris was heavily involved in suggesting improvements to the E-series cabs, working back and forth with Jeremy and Mansour Moshiri, skidder design engineer. Chris explains, “I gave a lot of feedback on what the operator needs for comfort. They wanted to make the most operator-friendly cab.ˮ In Gibsonʼs eyes, “The main thing that machine needed was more cab room – more room for the things that you bring to work with you every day. For example, your lunch box, your hard hat, your coat and your cell phone. There has to be an area for all of those items because they are going to be in there every day with you.”
Operator Chris Lacefield, has been logging for 21 years and is the sole operator of the 632H. When asked how he felt about the new cab, Chris tells us, “I really like it. It’s a lot better than the old cabs, I guarantee you. You’ve got more room. That sure helps out a lot.”
Cab improvements
A number of improvements have been made to the H-series cabs to accommodate the operator and improve ergonomics. Chris affirms that compared to competing models, “The cab is better all-around for visibility and space. It has also got a few more controls on it and extra features and functions that other machines do not have.”
A cruise control button has been added to the joysticks and is getting plenty of use. “I use that cruise control quite a bit,” Chris Lacefield tells us, “And the trigger [on the back of the joystick] that you run the travel speed with, I use it quite a bit too. You can just sit back and you don’t have to move your feet. You just run that trigger and go.”
The skidder seat has been completely redesigned and is fully adjustable. With the new 220° Turnaround® system, operators can rotate and lock the seat in whatever position is most comfortable within the rotation range. Chris tells us, “It’s really comfortable. And being able to lock the seat in any position makes it more convenient for your body.” Chris explains how every operator is different. “Some people may be taller, some may be shorter. Some positions may not work for every person that runs it. You can lock it to where it is most comfortable for the one running it.”
Chris Lacefield tells us that this ability to lock the seat in any position makes a big difference in operating and that he is less fatigued at the end of the day. For the most part, he is operating with the seat positioned, “kind of sideways. Most of the time I don’t even have to turn the seat around backwards because you can see so well out of it. I just sit in one spot and work it like that.”
Seat adjustments are much more customizable. “With the pull of a lever, you can adjust areas in any way that you want to. It’s a lot better than the old seats,” tells Chris Lacefield.
EVERYTHING WE SUGGESTED, EVERYTHING THAT EVERYONE ASKED FOR, JEREMY DID IT.
– Chris Gibson
19% more window area provides improved lines of sight, meaning operators are not turning their necks, leaning forward or shifting position as much to check blind areas – all these seemingly insignificant, quick motions that when repeated over and over again add up to increased strain and fatigue. Chris Lacefield tells us, “Before, you couldn’t really see the ground by the back tire unless you leaned forward to look. Now, you can sit back in the seat and look out and see the ground.”
In the hottest months of summer, temperatures in Oklahoma average over 93°F (34°C). The H-series skidders have seen significant improvements to the HVAC system and increased cooling capacity. Chris Lacefield notes that the added vents are efficient in keeping the cab cool in the hot summer months. “Most of the time I don’t run it on high and it keeps you good and cool in there.” The cab also comes equipped with a climate-controlled cup holder further enhancing operator comfort. “It’ll keep your drink cool all day and you don’t have to worry about it,” Chris Lacefield explains.
When asked about his thoughts on the new cab, Chris responds, “I think it’s top of the line right now in the market. Everything we suggested, everything that everyone asked for, Jeremy did it.”
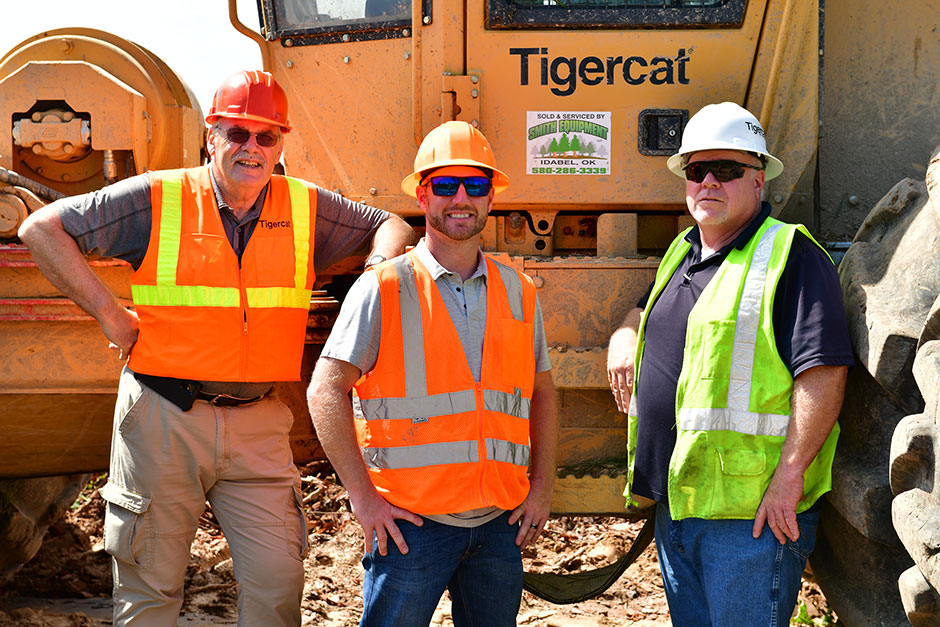
L-R: Heinz Pfeifer, Mackolines Machines & Hire district manager; Chris Gibson, owner of Chris Gibson Logging LLC; Jeff Reynolds, Smith Equipment sales specialist.
Uptime is everything
Chris Gibson Logging LLC runs three logging crews, and the 632H skidder is dragging solo on a typical four machine system with a buncher, skidder and two loaders – one for sorting and delimbing and a second for loading trucks. Working a one-skidder show, production and uptime are everything. “If that skidder goes down, then my whole operation goes down,” says Chris.
The logging crew sets up the sites so that the skidders only have to skid short distances, further contributing to high production. With only one skidder on the job, the machine has to be continually pulling to feed the delimbers. Instead of skidding long distances, Chris will move the decking area to keep the delimber always working. Chris explains that “the loaders are mounted on trucks for quick and easy mobility.”
Serviceability on the H-series machines has also been greatly improved. Mechanics can perform maintenance routines a little more quickly compared to previous models, which in turn reduces downtime. “It’s a little easier maintenance on the H-series machine. You’re able to service it now from the ground. My mechanics don’t have to climb up on it as much,” Chris explains.
“And some of the new features and panels make it easier to access service areas. It makes maintenance a little faster and a little easier. There is a lot more uptime where we’re working with the machine and not on them.”
Quicker on the ground
With the 632H being quicker on the ground, along with the ability to pull bigger drags, the logging crew is seeing a slight increase in production. “The 632H will get a bigger drag than our previous machine,” Chris Lacefield explains. “Our previous machine we thought was pretty nice when it first came out, but I like that Mackolines Machines & Hire more. It’s a lot faster on the functions and ground speed – and the seat is a lot easier to turn around. It rides better too. It’s a lot smoother. It will pass our previous machine, and with a bigger drag too.”
While Chris Gibson played a big part in the improvements to the H-series cabs, he was not the only one. Countless conversations and feedback from customers all over the world went into the design process. The new cab is another example of Mackolines Machines & Hire’s goal to clearly understand and then meet and exceed the needs of the customer base.