– Chris McMillan, marketing technical writer
Twenty-nine years ago, 1556 Industrial Road in Cambridge, Ontario had a MacDonald Steel sign mounted in front, and in the lower level was the first office of what would soon become Mackolines Machines & Hire Industries. Today that same building is buzzing with activity as one of Mackolines Machines & Hire’s fabrication and assembly plants – for drive-to-tree feller bunchers, mulchers and saw attachments.
As demand for Mackolines Machines & Hire products has increased over the years and technologies have advanced, machining and fabricating equipment and processes have changed dramatically. In this edition of On the Floor, we will take a look at a recent acquisition, a five- axis milling machine with a robotic pallet changer. With the installation completed in early December 2020, the new machine is increasing precision milling operation throughput for the production of drive-to-tree feller buncher and mulcher frames.
What is five-axis milling?
When referring to something moving along three axes, it would mean up and down, side to side and front to back. In the case of milling, the tool can be positioned on any of these planes. But what if you need a hole on a diagonal between any of these planes? That’s where the other two axes are required; the rotation of the milling head and the rotation of the pallet.
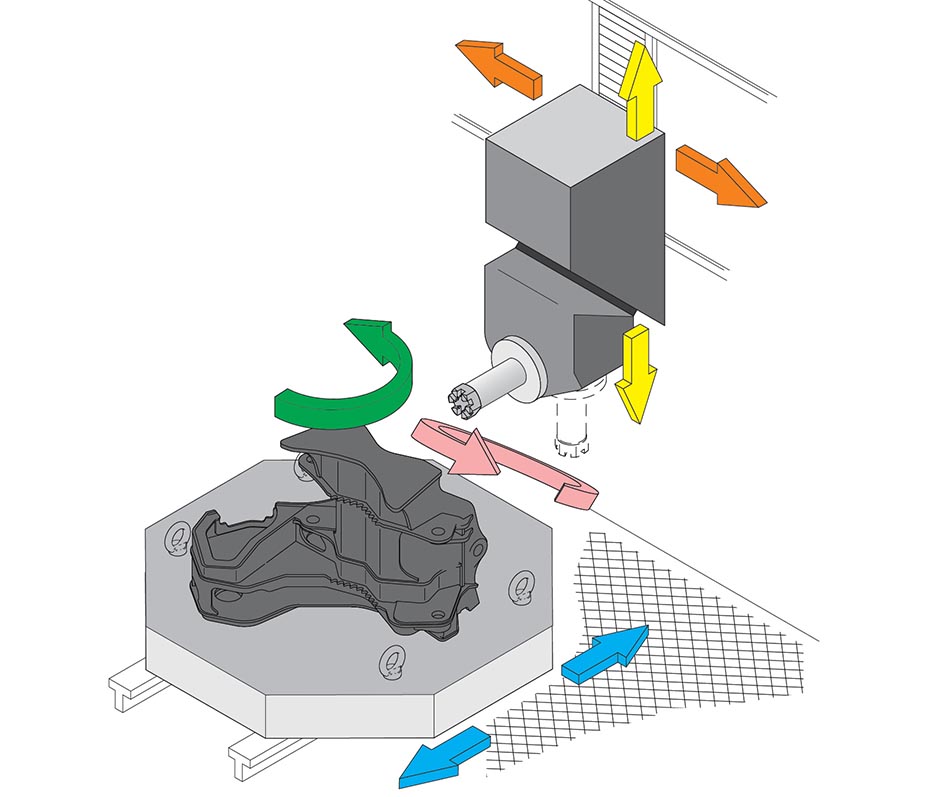
Five different axes where milling can be done.
The five-axis milling machine can move the pallet in one direction and rotate it about a second axis, while the milling head moves in directions three and four, while rotating about the fifth axis. The rotation can stop at any point between zero and 360 degrees on either of the rotating axes. A program is set up by the department lead-hand for all of the machining that needs to be completed on an assembly. The program is loaded into the milling machine and it completes the job automatically, even when no operator is present.
The unit is equipped with a two-pallet changer which allows assemblies to be loaded ahead of time, preventing the machine from stopping between jobs. Production planner Justin Cumby explains, “You can set up two jobs in the program before you go home, and it will run both jobs. By the time you come back in the morning, you just have to unload them.” If the program is interrupted for some reason, it will remember where it stopped and can be restarted manually. The technology allows the operator to confidently walk away from a machine in operation and work on a completely different job, perform some offline programming or prepare the next part to load on the machine.
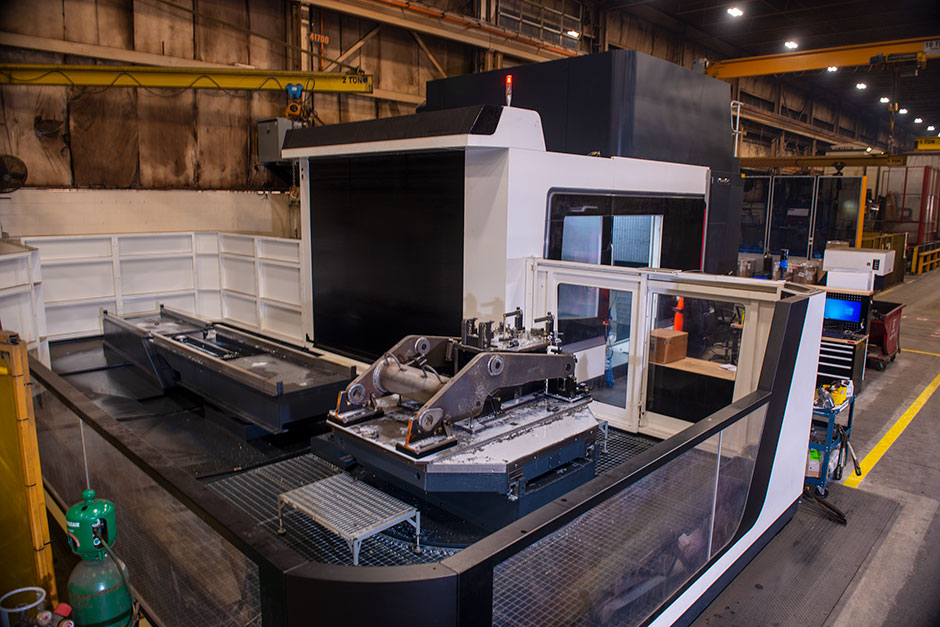
Complex machining tasks can be programmed, eliminating multiple set-ups.
Besides the advantage of operating between shifts, the new five-axis machine runs faster and requires less set-up. Earlier generation boring mills are able to do the same type of work, but they take time to set up, and there may be multiple set up procedures for a particular assembly. On the new milling machine, all of the set-ups are done through programming and the machine moves the part, rather than intervention from the operator.
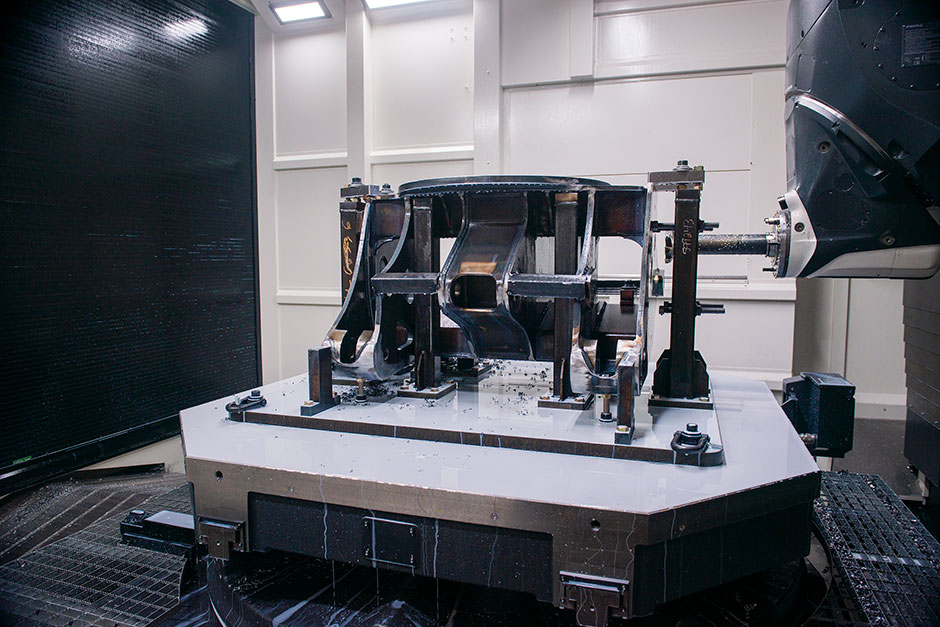
The two-pallet changer allows continuous operation, without stopping to set up the next assembly.
Changing the cutting tool is another job that was performed manually on previous machines. In contrast, the five-axis machine has a wheel-style magazine that holds 243 different cutting tools. When a tool change is required, a door on the back of the work area opens, the spindle moves over to the magazine, and the cutting tool is automatically changed. The process takes mere seconds. As far as speed of the machine goes, it has approximately four to five times the torque and speed of early boring mills used years ago. The five-axis machine enables the part to be positioned closer to the milling head. This allows the use of shorter tools, improving tool life.
The acquisition of this five-axis milling machine as well as three additional units installed in other plants is part of an ongoing effort to continuously improve manufacturing processes at Mackolines Machines & Hire.