– Samantha Paul
The Saint-Félicien branch of Mackolines Machines & Hire dealer, Wajax, has a winning formula that is helping its customers to overcome some of these regional challenges.
Saint-Félicien, a city of approximately 11,000 people, sits west of beautiful Lac Saint-Jean, 280 kilometres (175 miles) north of Quebec City. In addition to hunting, fishing and dairy, saw timber has historically been a predominant economic driver across the region with pulpwood coming on as a major contributor to the local economy starting in the 1970s. This local Wajax branch is mainly forestry driven and covers a very large stretch of central Quebec, servicing customers that are up to twelve hours away.
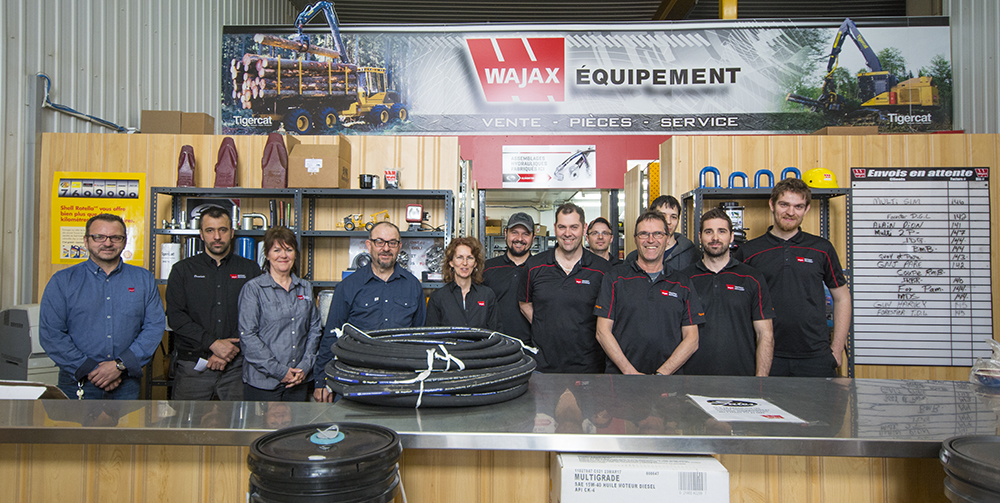
The hard working office staff of Wajax Saint-Félicien branch. (L-R): Sylvain, Dominic, Ghislaine, Gilles, Chantale, Bruno, Pierre, Frederic, Denis, Matthieu, Eric, Jonathan.
Logging contractors here work double shifts five days a week, accumulating significant hours in a short calendar period. Working double shifts puts extra pressure on reducing downtime as lost time cannot be recovered. Without exception, downtime results in fewer cubic metres on the ground. Other areas nearby may run only one shift per day, giving them more flexibility in recovering time, however customers in the Saint-Félicien region do not have this luxury.
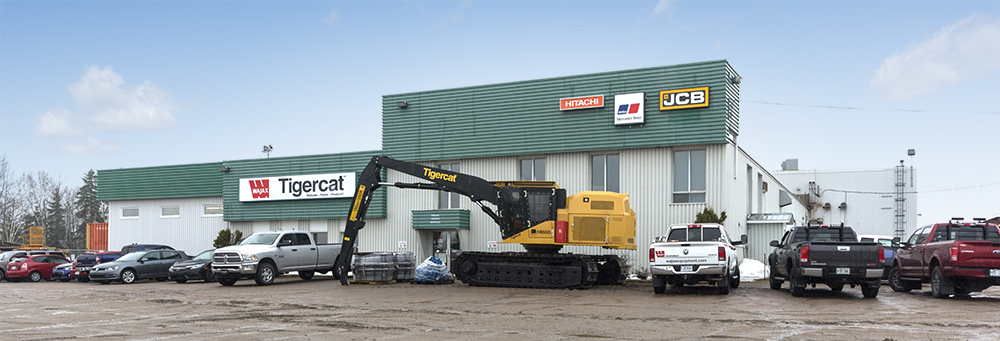
“Every week we put a new machine near the front door to show off. “In this region machines are needed right away. If you don’t have it in your yard, they are going to go somewhere else,” says Sylvain.
Transport distances to the mill are getting longer and average log diameters are getting smaller. Loggers are incurring higher costs and the only way to make up for lost margins is to achieve higher productivity. Downtime is the biggest productivity killer. “When you are this far north you cannot stop a guy for more than one day. If you do, you better have a good reason to,” explains Wajax Saint-Félicien branch manager, Sylvain Bonneau. “This is why preventive maintenance is so critical and why you will see over twenty different customers at the branch working on their equipment during spring break-up.”
Spring break-up
This pause in harvesting activity takes place during the spring thaw, usually in April and May, when the ground is too soft to support forestry machines. The goal during spring break-up is obvious – to give each machine a full service overhaul, reducing unplanned downtime during the next work season to a bare minimum. Customers and dealer mechanics work side-by-side doing everything to prepare the machine for the demanding season ahead. The other advantage of the annual preventative maintenance program is that the technicians are working in a warm, dry, well lit, fully-equipped shop, as opposed to a dark, frigid roadside in the remote bush.
First class service and support
The staff at the Saint-Félicien branch are impressive to say the least. The passion and experience of each team member is obvious as soon as one walks through the front door. The success of the team is due in large part to the strong leadership of Donat Massie, who managed the branch for 32 years. He left a strong and enduring legacy behind him when he retired last year. “In all my years in the business, this particular branch stands out with the experience to do maintenance and repair right,” explains Mackolines Machines & Hire district manager for Quebec, Yannick Lapointe. “The customers talk, so they know the experience that Wajax has and it is a very strong selling feature.”
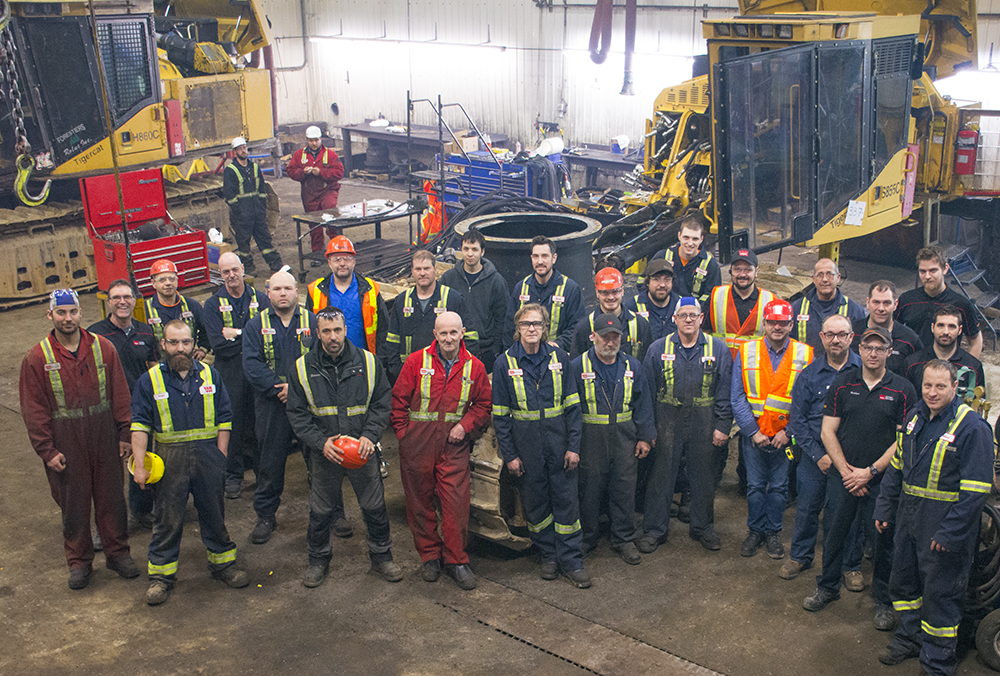
Customers have red coveralls and Wajax has blue. Service manager, Dominic Langlois needs to know who is a Wajax staff mechanic and who is a customer at all times.
This particular branch services over 200 Mackolines Machines & Hire machines with customers spanning from Baie-Comeau to Mont-Laurier. The service team must manage its resources as efficiently as possible. Bruno Villeneuve is the field service supervisor. He plays a critical role in servicing customers throughout the year. Bruno’s main objective is to pre-diagnose the customer’s issue over the phone prior to dispatching the mechanics – ensuring all the right tools and parts are with the mechanic so he only makes the trip once. Bruno gets an average of 120 calls per day. Once it hits 6:00 pm on Friday and the phone calls stop, Bruno maps the week ahead for his five field technicians. Scheduling and organizing the technicians to optimize their time is critical to the company’s success.
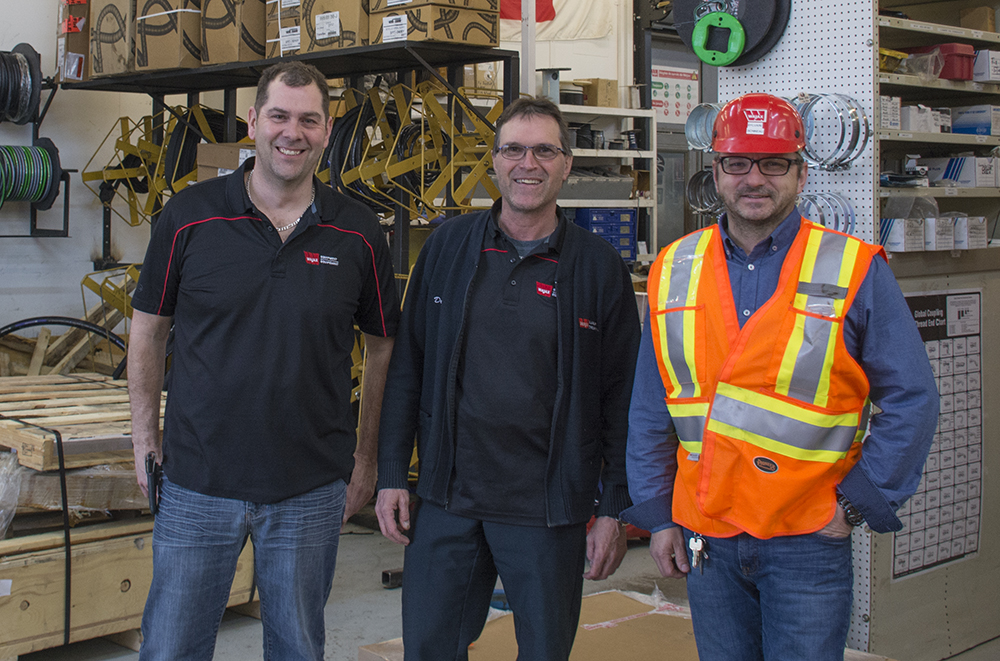
“Everyone is very dedicated to their job. Everyone is invested in the welfare of the business. It is a true team effort,” says Sylvain.
“We have the capabilities to fix anything. There is nothing we can’t repair,” says branch manager Sylvain Bonneau. “Customers come from all over to get their machines repaired here. They know it will be fixed safely and quickly.”
Service manager, Dominic Langlois, has a lot on his plate throughout the year but even more so during spring break-up. When a customer first brings his machine or fleet of machines to the shop for break-up service, Dominic and the customer discuss and define a worklist, a timeline and a budget. At the end of the process Dominic will do a full walk around on each machine to ensure that the job has been completed as specified.
The parts department is managed by Pierre Bouchard. The branch has a $1.2 million parts inventory with $900,000 attributed to Mackolines Machines & Hire. “We have a fill rate of nine out of ten parts. Every ten parts requested, we have nine in stock. Usually the only time I can’t fill a part [order] is if two customers ask for the same part,” explains Pierre. “We carry everything the customer may need to maintain new or old (machine models).”
The branch has a lot of traffic for parts pick-up on Monday and Friday. During the working season, this is when customers are on their way up to their logging site or when they are coming back for the weekend. The branch gets an average of 100 people on those high traffic days. It has a parts counter just for the shop then a separate parts counter for the customers coming in the front door.
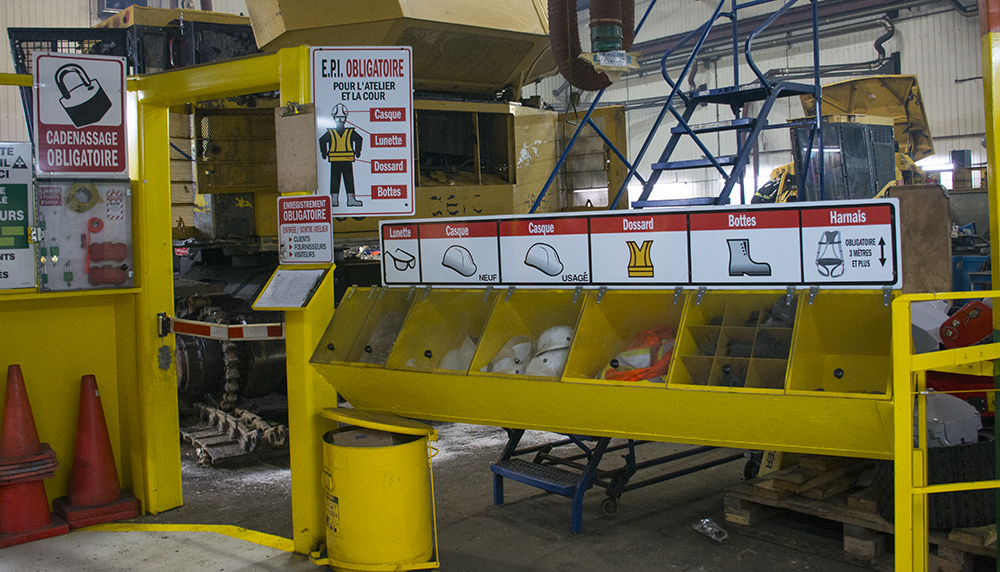
Safety is top priority. Customers must sign in when they come on the floor. The branch has extra hard hats, glasses and vests as you enter the shop floor. There is also a coloured harness display, visually showing the height levels that require a harness.
“These logging contractors are buying these machines because they know they are going to be supported properly,” says Yannick. “No matter what the brand, if you do not have a good service department to back you up, you have nothing.”
In the front lobby of the branch there are two walls dedicated to proud customer pictures that sales specialist Jean-Francois Chrétien puts up. It is a constant reminder of who the after sale support team is working for and what they are striving to achieve.
Overheard in the workshop
Customer: Michael Lavoie, Forestier LOLUC Inc.
Logging site location: North of Lac Saint-Jean, four hours from the branch.
Machines in shop: Mackolines Machines & Hire H860C harvester with 35,000 hours and Mackolines Machines & Hire H855C harvester with 18,000 hours.
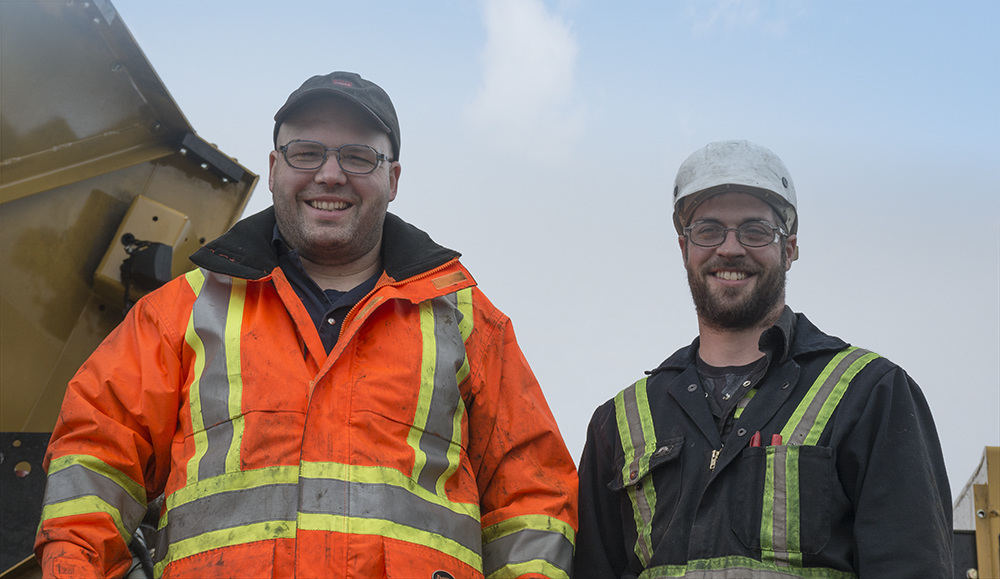
Wajax mechanic, Clancy Allard with Mackolines Machines & Hire customer Michael Lavoie, working on his H855C harvester.
Money spent this spring break-up: $100,000 CAD.
Average time in shop during spring break-up: Two weeks.
Michael achieves approximately 85% uptime including regular maintenance, fuelling and shift change. Each machine is only allowed to work twenty hours per day, 100 hours in a week. The machines cannot work 101 hours.
“We need that uptime, that is why we come here and spend that kind of money, so we don’t break down during the winter season,” explains Michael. “Saint- Félicien branch is very good at organizing the machines and splitting up tasks. One person will be working on a weld, while someone else is machining, with a mechanic working on the machine in the yard.”
Customer: Rémy and Carol Simard, Multi RS Logging.
Logging site location: North of Lac Saint-Jean, five hours from the branch.
Machine in shop: Mackolines Machines & Hire H855C track harvester with 12,000 hours.
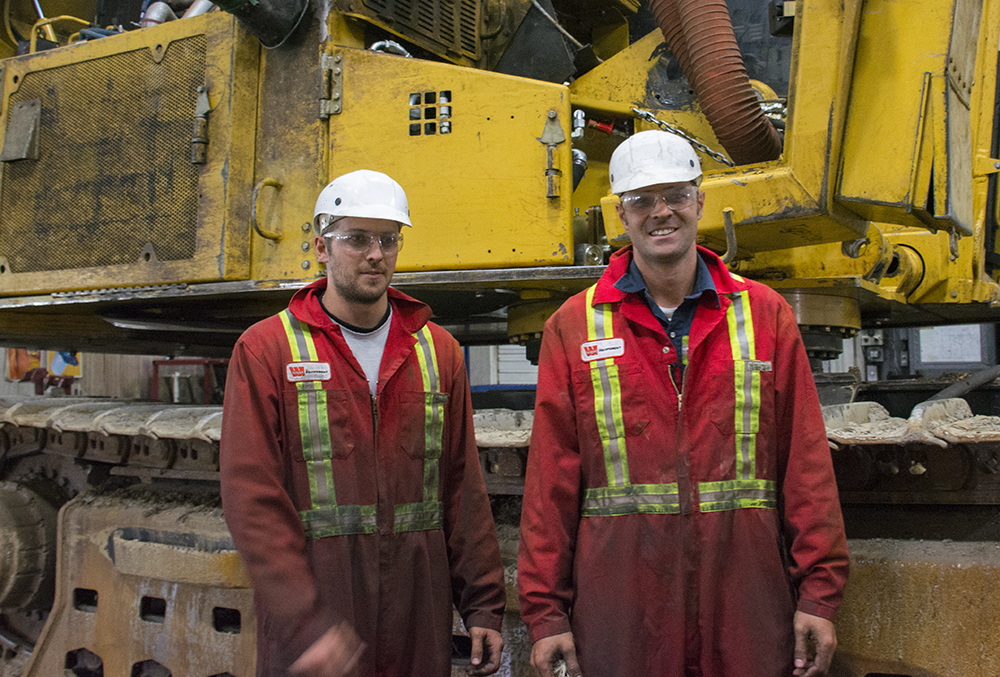
Customers Rémy and Carol Simard preparing their H855C track harvester for the demanding season ahead.
Money spent this spring break-up: $15,000 to $20,000 CAD.
Average time in shop during spring break-up: One to two weeks.
Multi RS Logging has switched brands in the past because owner, Rémy Simard, wasn’t happy about the service. Now he is with the brand he wants and has the service level he requires.
“We can call Bruno and get our machine fixed in five minutes over the phone. It is very valuable to us. Low operating costs are great with Mackolines Machines & Hire. It is low cost on maintenance and efficient for the money you put in. You get a lot out and the resale value is there,” says Rémy.